silicon carbide briquette for steelmaking
Application of Silicon carbide briquette: With the development of the iron and steel industry, the iron and steel industry has put forward higher and higher requirements on the productivity of steelmaking and the cost of steel. At present, due to the smelting process of most steel mills, the temperature of the converter iron and steel water is relatively low, and the content of sulfur and phosphorus is relatively high. The steelmaking often needs to blow oxygen many times due to insufficient heat. Achieving sufficient tapping temperature will result in high oxygen activity of the molten steel at the end point and high total iron content in the slag, which will adversely affect the smelting steel grade and converter age, and is not conducive to the economics of steelmaking. At present, the more commonly used methods in domestic converter steelmaking thermal compensation technology have used coke, anthracite and other heating materials successively, but they have been eliminated one after another due to their large defects. The carbon content of steel also plays a certain role in alleviating the shortage of heat source for semi-steel steelmaking, but its pertinence is not strong and the cost is high. At present, in order to optimize the steelmaking logistics and reduce the production cost, a new temperature-raising material (SiC briquette) with fast melting, good heating effect and easy operation is urgently needed to replace the existing coke and anthracite. Equal heat compensation materials in order to better solve the converter heat compensation technology to meet the technical requirements of steelmaking short process production.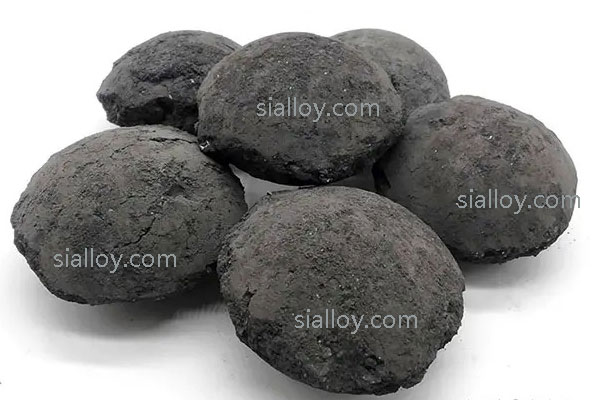
Silicon carbide briquette is a new type of temperature-raising material, that is, a high-efficiency and low-sulfur steel-making deoxidizer. Silicon carbide briquette is prepared from the following raw materials by weight ratio: 85-90 parts of silicon carbide powder, 5-10 parts of lime, and 1-3 parts of binder. Wherein, the silicon carbide powder contains 2-10% carbon by weight, more than 50% silicon carbide (preferably 50-70%), 0.1-0.3% sulfur (the remaining components are irrelevant element content and impurities), lime Calcium oxide > 90% by weight, and the binder is a binding material. Sodium bentonite has slow water absorption speed, but large water absorption rate and expansion ratio; high cation exchange capacity; good dispersibility in aqueous medium, high colloidal price; its colloidal suspension has good thixotropy, viscosity, lubricity, and high PH value ; Good thermal stability; high plasticity and strong adhesion; high hot and wet tensile strength and dry compressive strength. Therefore, the use value and economic value of sodium bentonite are relatively high. Guangxi white mud contains 25-35% aluminum oxide and 40-55% silicon dioxide by weight. Sodium carboxymethyl cellulose is the sodium salt of cellulose carboxymethyl ether, white powder, anionic cellulose ether, particle size -200 mesh, purity > 90%, referred to as CMC. CMC is usually an anionic polymer compound prepared by reacting natural cellulose with caustic alkali and monochloroacetic acid. Dextrin is a degradation product obtained by enzymatic or chemical hydrolysis of starch, and is a mixture of oligosaccharides and saccharides with several to dozens of glucose units. Among them, the particle size of silicon carbide briquette is 10-50mm. Among them, Silicon carbide briquette contains < 3% moisture by weight.
Application of SiC briquette as a warming agent in converter smelting process. Specifically, during the converter smelting process, Silicon carbide briquette can be added from the top of the converter as a temperature raising agent. The method of adding Silicon carbide briquette is simple and convenient. Adding 7-9kg of Silicon carbide briquette per ton of molten steel in the converter smelting process has obvious effect of temperature increase, and can increase the amount of scrap steel, reduce the dependence of converter steelmaking on molten iron, and speed up the production and smelting cycle.