carbon additive for casting
Carbon additive for casting can divided into graphitized petroleum coke, calcined coal, columnar graphite, calcined petroleum coke according to different raw materials, for different castings will need different content of sulfur, then can choose different carbon additive according to the requirement of sulfur. After adding carbon additive in the casting process, the amount of scrap steel can be greatly increased, and the amount of pig iron can be reduced or no pig iron is used.
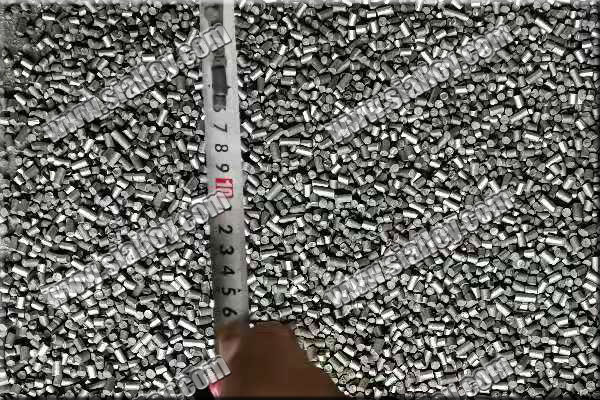
1.How to choose the carbon additive for casting?
Generally, the sulfur content of the carbon additive used in gray casting will be low, and the sulfur below 0.5 can be used normally, and the requirements are not so strict. The absorption rate can be achieved. Ductile iron has strict requirements. It not only requires fixed carbon content, but also requires low sulfur and low nitrogen. Otherwise, the produced castings are prone to brittleness and cracks, which will greatly affect the final effect. Nitrogen must be low in nitrogen, preferably 600ppm or 300ppm. The lower the nitrogen, the smoother and smoother the castings are without pores. The higher the nitrogen, the more uneven the castings, and some even have pores and cracks.
2.How to use the carbon additive for casting?
Generally, the carbon additive is put into the furnace together with the scrap steel and other charges. The addition of small doses can be added on the surface of the molten iron, or it can be added quantitatively in batches. (Note: Avoid feeding large quantities of molten iron to prevent excessive oxidation, resulting in insignificant carburization effect and serious damage to castings.)
Anyang Huauto Metallurgy Co.,ltd has in various type of carbon additive for casting for more than 10 years, and the characteristics of carbon additive they supplied as following:
(1) The amount of pig iron is greatly reduced, and the cost of castings is greatly reduced.
(2) High temperature roasting, graphitization, high fixed carbon content.
(3) The quality index is stable and the content of harmful impurities is low.
(4) High absorption rate (8-90%), no residue, more environmentally friendly.
(5) No slag is returned, and the working conditions are easy to control.
(6) There are many graphite nuclei and good graphitization, which reduces the shrinkage tendency of molten iron and improves the mechanical properties of castings.
(7) Complete series of specifications, product granularity can be adjusted according to customer requirements.
If you have the confused about carbon additive welcome for consult.