recarburizer for steelmaking
How to choose recarburizer for steelmaking
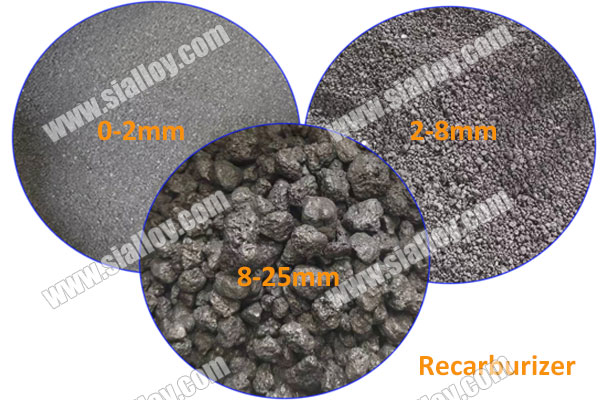
1.The fixed carbon and ash in recarburizer for steelmaking
When the recarburizer with high fixed carbon content and low ash content uses in the steelmaking plant, the carburizing effect is good, otherwise, the carburizing efficiency is poor. When the ash content is high, it can inhibit the content increase, which will increase the amount of slag, prolong the operation time and increase the power consumption of smelting.
2.How to add recarburizer for steelmaking
The addition method of the recarburizer used in the steelmaking plant has a great influence on the carbonization efficiency. After mixing, it is placed on the bottom and middle of the induction furnace. This method of adding is more efficient than adding a recarburizer after adding the charge.
3.Sulfur content of recarburizer for steelmaking
When smelting ductile cast steel, it is better to use recarburizers with low sulfur content in steelmaking plants. Some customers feel that the price of low-sulfur recarburizers is not cost-effective, but it must be necessary, because if it is used when smelting gray cast iron The recarburizer used in steelmaking plants with high sulfur content can reduce costs and enhance the response of molten iron to inoculation treatment, thereby producing castings with high metallurgical quality.
The way to use recarburizer for steelmaking
1.Furnace input method
The recarburizer is suitable for smelting in the induction furnace, but the specification use varies according to the process requirements.
(1)) The recarburizer used in the intermediate frequency electric furnace smelting can be added to the middle and lower parts of the electric furnace according to the ratio or carbon equivalent requirements, and the recovery rate can reach more than 95%;
(2) If the carbon content is insufficient to adjust the carbon content, first clean the slag in the furnace, add a recarburizer, heat the molten iron, electromagnetic stirring or manual stirring to dissolve and absorb the carbon, and the recovery rate can be about 90%. The low-temperature carburizing process is adopted, that is, only part of the charge is melted, and when the temperature of the molten iron is low, all the carburizers are added to the molten iron at one time, and at the same time, the solid charge is pressed into the molten iron. In this method, the carburization of molten iron can reach more than 1.0%.
2.Furnace output method
(1)Spraying graphite powder in ladle
Choosing the graphite powder as recarburizer, the blowing amount is 40kg/t, which is expected to increase the carbon content of the molten iron from 2% to 3%. As the carbon content of molten iron increases gradually, the utilization rate of carbon content decreases. The temperature of molten iron before carbonization is 1600 °C, and the average temperature after carbonization is 1299 °C. To increase carbon by spraying graphite powder, nitrogen is generally used as the carrier, but under industrial production conditions, it is more convenient to use compressed air, and the combustion of oxygen in the compressed air produces CO, the heat of chemical reaction can compensate for part of the temperature drop, and the reducing atmosphere of CO is conducive to Improve carbonization effect.
(2)Use recarburizer when tapping
The 100-300 mesh graphite powder recarburizer can be put into the ladle, or flushed from the tapping slot with the current, and fully stirred after the molten iron is discharged, so that the carbon can be dissolved and absorbed as much as possible, and the carbon recovery rate is about 50%.
Anyang Huatuo Metallurgy Co., Ltd has in various types of recarburizer for more than 10 years, if you have any confused about recarburizer welcome to consult us.