CaSi Cored Wire
CaSi Cored Wire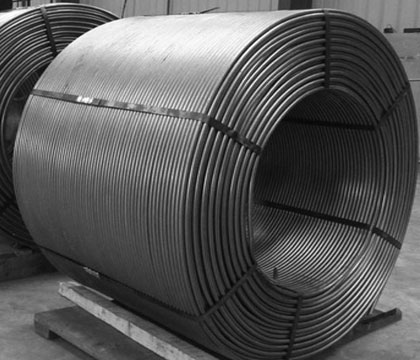
- Name: CaSi Cored Wire
- Model: CaSi:6030/5528
- Size: Diameter 13mm
- Shape: Cored Wire
- Usage: Deoxidizer, Desulfurizer for Steelmaking
The main raw material for the production of Casi cored wire is Calcium Silicon alloy. The crushed calcium silicon powder is used as the core material, and the outer skin is cold-rolled steel strip. It is pressed by a professional crimping machine to make the silicon-calcium cored wire. In the process, the steel sheath needs to be tightly packed to make the core material fill evenly and without leakage.
The Spcifications of Cored Wire
Model | Chemical(%) | Wire diameter | Wire Thickness | Wire weight | Powder Weight | Uniformity (%) |
---|---|---|---|---|---|---|
SiCa | Si60Ca30 | 13mm | 0.4mm | 170g/m | 230g/m | 2.5-5 |
CaSi | Si55Ca28 | 13mm | 0.4mm | 170g/m | 230g/m | 2.5-5 |
The usage of Casi cored wire is mainly for steelmaking. It is mainly used for deoxidation and desulfurization in the steelmaking process. Compared with other methods of deoxidizing and desulfurizing materials, the Casi cored wire is developed. Developed with higher quality alloy steel and variety steel, the Casi cored wire can improve the performance, plasticity, impact toughness and molten steel flow in all aspects of steel.
The use of the wire feeding technology to use the Casi cored wire has greater advantages than the powder spraying and the direct addition of the alloy block. The feeding line technology can effectively put the Casi cored wire into the ideal position in the molten steel, effectively changing the inclusions. The shape of the material improves the castability and mechanical properties of the molten steel.