usage of silicon carbide in iron casting
Silicon carbide is a compound consisting of one carbon atom and one silicon atom, with 70% silicon and 30% carbon (by weight). It was accidentally discovered by Edward G Acheson while making synthetic diamonds. Its original use was as an abrasive because of its hardness and ability to cut glass, metal, and other materials. Since it does not oxidize at almost any temperature, it can be used as a refractory. Since it is also very stable at high temperatures, it has been widely used as a kiln filler. Because of its resistance to slag erosion, it can be used as a slag line brick for aluminum smelting furnaces and blast furnaces. Since it dissolves in the presence of slag, carbon atoms and silicon atoms will be released as charged ions (C-4 and Si +4), so it is an effective deoxidizer widely used in electric furnace steelmaking. .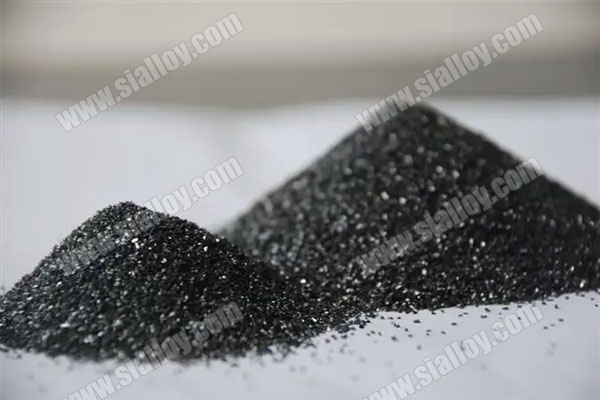
When it is added to gray, ductile or malleable iron, it not only dissolves easily, but also alloys carbon and silicon into the melt. When the temperature is lower than 1620℃, its carbon will act as a deoxidizer, so that less stable oxides such as FeO and MnO are reduced by the reaction of SiC+FeO=Si+Fe+CO. When the temperature is higher than 1620 ℃ (such as in steelmaking), silicon will undertake all the deoxidation tasks, while carbon will act as a recarburizer, and its yield can reach 100%. Coreless induction melting of iron is the main field of application for silicon carbide. About 95% of coreless induction furnaces in the United States use SiC as the primary silicon source. In terms of gray iron, ductile iron and malleable iron, SiC is used to reduce the content of FeO and MnO in the slag through the reaction of SiC+FeO=Si+Fe+CO. Since the presence of FeO can lower the melting point of any slag, more of the slag becomes liquid at any given temperature because of the lowering of the melting point of the slag. For example, when the FeO content in the slag is 10%, its melting point will be 1350-1400 ℃, and under the strong stirring action of the coreless induction furnace, this liquid slag will be "homogenized" in the melt, As a result, thousands of very small slag particles are left in the melt, and many surface defects of the casting are the very fluid high FeO and MnO slag (usually called manganese silicate slag) that is brought into the mold. Caused. If SiC is added to reduce the FeO content of this slag to 1 or 2%, its melting point will be raised to 1500-1550 ° C, then, at the usual tapping temperature (1500-1550 ° C), this slag or Remains solid, or only a small amount becomes liquid, leaving a larger monomer in the furnace, which allows the slag particles to be easily ejected due to their higher uplift velocity and to be carried with them The chances of casting defects are greatly reduced.
The presence of very small FeO-SiO2 inclusions (fayalite) in the molten iron is the main reason for the decrease in the fluidity of molten iron, the increase in shrinkage tendency and the increase in white mouth, especially for ductile iron. Therefore, reducing its amount in the molten iron can eliminate the tendency to increase shrinkage and white mouth.