the interaction between metal fluid and iron mold
Metal fluids are thermally, physically, chemically, and mechanical effects during filling iron mold and solidification. Due to these effects, castings may produce cast defects such as sandwich, sand eye, air pores, viscopaste, surface oxidation or de-carbon.
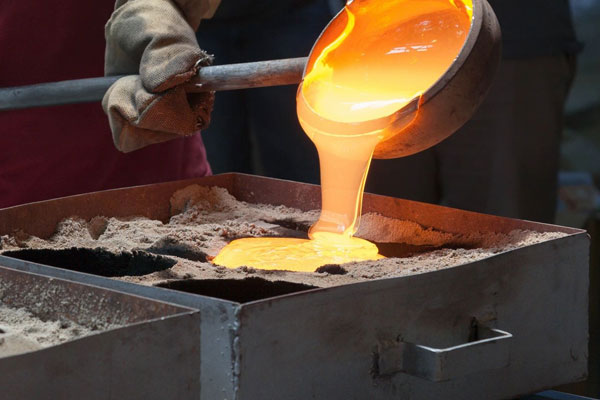
1.Thermally effect
(1)The mold moisture migration and cast strength change. The moisture in the sand-type surface layer is thermally evaporated, and the gap in the sand type is condensed, and the temperature is moved at a low temperature, and the intensity of the mold is changed.
(2)The mold produces expansion and stress deformation. The expansion and stress when the mold is heated and the stress is not only related to the material of the mold itself, the type of binder and the additives added, but also related to factors such as the heating temperature, heating speed, and the external conditions of expansion. When the thermal stress generated by the sand-shaped surface layer is thermostatic, the sand-shaped surface arch is cracking, which is the main cause of casting sand. Coal powder, residue, wood chips, etc. can be added to increase the inclination of sand type, reduce hot press stress; use sodium-based bentry soil or activate the calcium-based bunting soil to improve the hot and moisture strength of the sand.
2.Physically and chemically effect.
The physics, chemical effects between metal fluids and molds are present, and a large amount of gas is evaporated and organic matter, carbonate decomposition or the like; metal liquid is infiltrated into a cast surface void; metal liquid and cast material A chemical reaction occurs at high temperatures to form a compound of the low melting point or the like. These acts cause flaws such as pores, viscaps, and surface oxidation or de-carbon castings.
The metal fluid reacted in the formation of the ferrous oxide (FeO) formed in the casting process to form a low-dissolving molten iron, wet silica sand, and penetrate into the sand (core) surface void, producing chemical viscosacial. An additive capable of combustion to form a reducing atmosphere can be added to the sand, and the addition of the reducing atmosphere can be added to reduce metal oxidation and reduce the degree of viscaslation.
The sintered point of the original sand or excess of clay is too much, in the case where the casting temperature is too high, the thickness of the casting is too large, and the surface of the cavity is easily sintered at high temperatures to form a thermal flapping layer. The main measure to prevent thermal inclusions is to use high-resistant zirconia, magnesium sand, chromium iron ore, or the coating coating cavity surface.
3.Mechanical effect
The cavity surface sand or coating layer falls off under a flow of metal fluid friction or dynamic pressure, such as a defect such as sand, slag air hole, and polyphae. To prevent sandblast, except for increasing the surface strength of the sand, it should be designed reasonably.
In order to product high qualitity casting, there are other effect except the above introduction, such as the qualified additive materials, recarburizer, inoculant, spheroidizing agent, etc, we Anyang Huatuo Metallurgy has in the raw materials of casting and steel-making for more than 10 years, hoping that we can help you with our experience before.