the effect of copper in cast iron production
In the iron-copper system, copper can be dissolved in a large concentration of liquid solid solutions with the iron solution. At room temperature, the solubility of copper in iron is small. Whether it is liquid or solid state, copper has a copper phase when the amount of copper exceeds each temperature. Copper is between 3-5% between the solubility of the molten cast iron, and the elements such as manganese, aluminum, and nickel in cast iron increase the solubility of copper, while magnesium reduces the solubility of copper. With magnesium, more than 2% of copper, that is, 97% of copper copper copper copper.
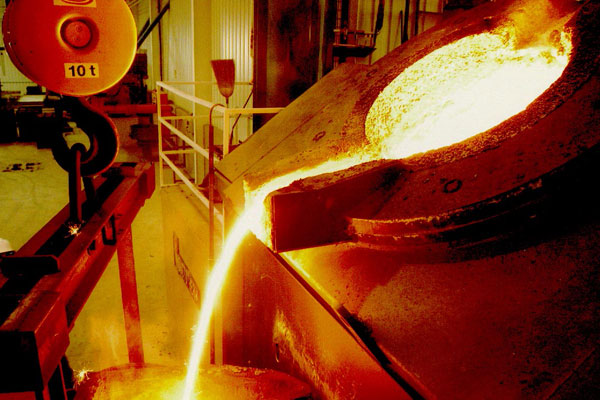
Copper has little effect on the temperature of cast iron. Copper belongs to a weak graphite element, which can slightly reduce the tendency of white mouth. Copper reducing the resolution temperature, approximately 1% copper, decreased by 6-10 ° C, which is stable. Copper can also increase the number of pearlescents, refine the eutectic group, and make the cast iron more easily to obtain pearlite tissues when normalizing. Therefore, copper promotes austenite generated pearlite in the circulation to prevent the action of graphitization. Copper can also strengthen ferrite and improve its strength. When the copper content is 2.0% or less, there is no significant effect on the spheroidization rate, the number of spheres, and the spherical size can ensure that the spheroidization rate is more than 90%. When the copper content exceeds 2%, the spherination effect is affected, the spheroidization rate is dramatically decreased, and the number of balls decreases sharply. When the copper content reaches 2.5%, a bulk graphite and yellow copper phase occur. Copper-resistant melting point is lower than the iron water temperature. After graphite precipitation, copper phase may enable graphite to gradually turn the graphite from the spherical shape.
The effect of copper on the spheroidization effect is related to the size thickness of the casting, and the casting of the wall thickness of 300 mm is added to the copper 3-4% to eliminate the agglomerate graphite in the core of the casting. It should be noted that this effect of copper is only effective when it is added with the rare earth element. Copper promotes the ball ink cast iron to generate pearls, and its ability is 10 times higher than nickel, but only 1/10 of tin. About the trial is added to 0.5% to 90% of the pearlescent volume in the ductile iron test rod in the φ25 mm ink, and the gallery content is added to 100%; and the ferrite occurs when more than 1.5%. This good role of copper allows people to obtain cast pearlescent bulky cast iron without heat treatment.
The effect of copper on the performance of gray cast iron. When the amount of copper is added to 0.5% or less, the tensile strength, yield strength, and the elastic modulus are increased, but it is not linear. When the ash cast iron contains about 0.8%, the strength is the highest, with the increase of copper, the impact toughness of the ash cast iron is lowered. Copper through promoting the generation of pearls and the mechanical properties of the metal-ink cast iron. Add a small amount of copper (0.5%) of the pearlite content has increased dramatically, tensile strength, yield strength and hardness have also increased sharply and the elongation has dropped sharply. The addition of more than 0.5%, the substrate has been all pearlite, but the strength, the hardness continues to rise, the elongation is no longer decreased. This is because copper makes the metal matrix to be strengthened. The role of copper has a fine graphoon, and the fatigue strength of copper-containing ball ink cast iron can be improved. The solid solution of copper in cast iron was 0.35% at room temperature, and 0.5% or more copper was added to the austenite and the diffusion velocity of the carbon atom during austenitic transition, promoting the formation of a pearlite and refined the pearlite. When the casting is cooled, copper precipitates from the solid solution to strengthen the matrix, significantly increase the microhardness of the pearlite. Increase the copper content to increase the wear resistance of the castings, when the destination annealing treatment, copper not only does not reduce the hardness, but also increases HB10 degree.