the cold crack of the casting
Cold cracking is the cracking caused by the local casting stress greater than the ultimate strength of the alloy when the casting is cooled to an elastic state after solidification. Cold cracks always occur in the parts that are subjected to tensile stress during the cooling process, especially the parts where the tensile stress is concentrated. Cold cracks are different from hot cracks. Cold cracks often extend transgranularly to the entire section, and the shape is straight or folded with uniform width and slenderness. The fracture surface of cold cracks has a metallic luster or is slightly oxidized. rather than along grain boundaries. This is significantly different from thermal cracking. Cold crack inspection is visible to the naked eye, and can be distinguished from hot cracks according to its macroscopic morphology and microscopic characteristics of transgranular expansion.
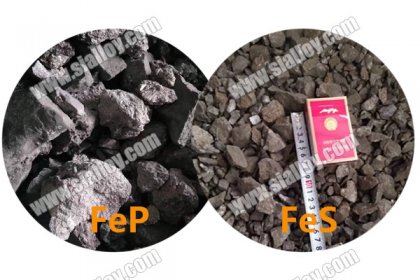
The main reasons for the occurrence of cold cracks are as follows:
1.Castings structure
The uneven wall thickness of the casting promotes the casting stress and sometimes cold crack defects. Castings with rigid structures are prone to thermal stress due to their structural obstructions, resulting in cold cracks in the castings. For example, a box-shaped casting with a "thin-walled and large-core" uniform wall thickness will produce temporary shrinkage stress due to the obstruction of the sand core. When the tensile strength of the alloy material is exceeded, the casting will be cold cracked.
2.The design of the pouring and riser system is unreasonable.
For castings with uneven wall thickness, if the inner gate is arranged in the thick wall part of the casting, the cooling rate of the thick wall part of the casting will be slower, resulting in or aggravating the difference in the cooling speed of each part of the casting, increasing the thermal stress of the casting , prompting the casting to produce cold cracks. Improper setting of the pouring riser directly hinders the shrinkage of the casting and also promotes cold cracks in the casting. Since the gate is thinner than the casting, the gate is solidified first, and when the inward shrinkage of the casting is hindered by the gate, tensile stress is generated, and cold cracks are usually prone to occur on the wall between the two gates. Secondly, the high temperature strength or dry strength of the molding sand or core sand is too high, and the high temperature concession is poor, which hinders the shrinkage of the casting, generates a large tensile stress, and causes cold cracks in the casting.
3.The chemical composition of the alloy material is unqualified.
The high content of carbon and other alloying elements in steel makes castings prone to cold cracks. Ductile alloy materials are not prone to cold cracks, while brittle alloy materials are prone to cold cracks. Phosphorus is a harmful element in steel. When it contains ω(P)>0.05%, it increases the cold brittleness of the steel and is prone to cold cracks. In gray cast iron, the presence of excessive anti-graphitization elements can also cause increased shrinkage of the casting, resulting in cold cracks in the casting.
4.Control the unpacking time
The casting is unpacked too early, the temperature of the falling sand is too high, and collision and extrusion during sand cleaning will cause the casting to crack.
In order to produce qualified casting, except to notice the process of production, the qualified raw materials also important, Anyang Huatuo Metallurgy Co., Ltd in various types of raw materials such as inoculant, spheroidizing agent, carbon additive, etc, if there are any interests just consult us.