sticky sand defects on the surface of sand castings
The sticky sand defects on the surface of sand castings can be divided into mechanical sticky sand and chemical sticky sand. Mechanical sand sticking is caused by molten metal drilling into the pores between the sand grains of the sand mold. Chemical sticking is a chemical reaction between SiO2 in the sand mold and metal oxides such as FeO to form ferrous silicate (ferroolivine) and adhere to the casting. The chemical composition of ductile iron castings is high in carbon, no ferrous silicate is produced, and the sticky sand produced is only mechanical sticky sand.
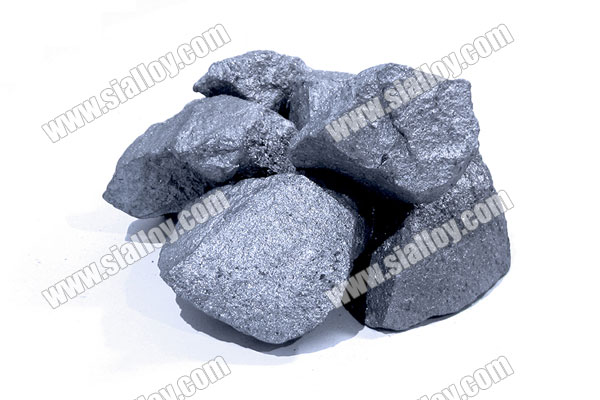
1.The production of large pieces of ductile iron with sticky sand uses clay dry, resin sand, and sodium silicate sand. High-quality coatings of refractory aggregates such as zircon powder, chromite powder, brown corundum powder, magnesia powder, graphite powder, etc. are usually used for pouring larger castings. However, in order to save production costs, paint manufacturers may add too many inexpensive materials such as quartz powder, bauxite powder, and coke powder to the powder, which will reduce its anti-sticking effect.
2.Most of the sand in the wet medium and small nodular iron castings contain coal powder, which produces a large amount of reducing gas during casting, which will not cause chemical sand adhesion.
Following discuss the influence of various factors on mechanical sand sticking and the solutions respectively.
(1)The degree of compaction of sand molds The degree of compaction of manual molding and seismic pressure molding is generally low. The sand particles on the surface of the sand mold are relatively loose, and the molten metal is more likely to penetrate the pores between the sand particles. The pits and corners of the sand mold cavity There may also be looseness everywhere. Workers can use their fingers to plug tightly, and use the tip of a hammer to squeeze locally. Whether the high-productivity and high-density molding has local looseness depends on the fluidity of the molding sand. Therefore, many factories try to reduce the compaction rate of the molding sand to improve the fluidity of the molding sand. It is very effective to use microseism in the sand adding and compaction process. In addition, it also depends on the setting of the compaction pressure of the molding machine.
(2)Pouring temperature The molten metal temperature is high and the fluidity is good, it is easy to penetrate into the pores between the sand grains to produce mechanical sand and rough surface. However, in consideration of avoiding defects such as porosity and cold barrier in the casting, the pouring temperature cannot be arbitrarily lowered. In the production of complex thin-walled castings, higher pouring temperatures are particularly required.
(3)The granularity and permeability of the molding sand. On the one hand, the thickness of the wet sand should be ensured smooth exhaust after pouring. On the other hand, the air permeability of the wet sand should not be too high to prevent the molten metal from easily penetrating into the pores of the sand. There are many vent holes in the sand molds for small parts produced by hand molding, and surface sand is often used. The sand particles can be finer, and the air permeability of the molding sand is 30-60. The grain size of the machine-molded green sand is roughly 70/140 mesh, and the air permeability is mostly in the range of 60-90. High-density sand molds are denser, and higher air permeability is required. The particle size is mostly 50/140 or 140/50 mesh, and the air permeability is mostly concentrated in 100-140. Normally, the grain size of the raw sand used for the sand core of the internal combustion engine casting is 50/100 mesh, which is coarser than the molding sand. In long-term production, a large amount of core sand will be mixed into the molding sand to make the particle size of the molding sand coarse, resulting in the air permeability of some factories as high as 160 or more. Unless paint is sprayed on the surface of the sand mold, the surface of the casting will appear rough or even localized mechanical sand. If the particle size of the molding sand becomes coarse, some foreign factories add new fine-grained sand of 100 mesh and 140 mesh when mixing the sand to correct it.
(4)The sand mould coating machine moulds larger wet ductile iron castings of more than 100 kilograms. The lower sand mould can be sprayed with alcohol-based paint, and the core can be set and moulded after being ignited. Generally, the upper type does not need to spray paint, because the metal hydraulic head is smaller than the lower type. Another advantage of spray coating is to improve the erosion resistance of the sand surface.
When using resin cores or oil sand cores to produce general ductile iron cast iron that does not require high internal cavity, in order to prevent molten metal from drilling into the sand core, you can apply machine oil or other parts on the surface of the hardened sand core where the molten metal is easily penetrated. Coating paste prepared by binder and graphite powder, quartz powder or other refractory powders can be cored after cooling dry. When producing cast iron parts (such as internal combustion engine cylinder heads, body, hydraulic system valves, etc.) that require high internal cavity cleanliness and smoothness, the sand core must be coated with an overall coating and then dried on the surface. When producing small ductile iron parts by hand, a soft brush is often used to carefully paint the graphite powder on the surface of the wet sand mold and sand core. Some are sprayed with a mixture of graphite and water, and poured after natural drying. Graphite powder can fill the pores and is not wetted by the molten iron, which makes it difficult for the molten iron to penetrate between the sand grains.
(5)Explosive sticky sand can sometimes see sticky sand defects on the upper surface of the casting position of the casting, which is different from the usual sticky sand on the lower surface of the casting position. This is caused by an explosion when the molten iron level is adjacent to the upper surface of the cavity. At the beginning of pouring, the moisture of the sand mold evaporates and condenses on the upper surface of the cavity with a lower temperature. When the metal liquid level rises and comes into contact with the upper surface of the cavity, the moisture suddenly evaporates and explodes. When the molding sand has high water content and pulverized coal content, the sand mold has poor aeration conditions and the pouring speed is too fast, explosive sand sticking is more likely to occur.
(6)The amount of pulverized coal in molding sand The most important molding sand additive for wet cast iron parts to prevent sand sticking and improve the surface finish is pulverized coal. However, there are mixed results of commercially available pulverized coal.