spheroidizing agent of ductile iron
At present, conventional ductile iron, that is, ductile iron based on ferrite and pearlite, still accounts for most of the production of ductile iron. Therefore, attention should be paid to improve the performance and quality of conventional ductile iron to maintain the competitive position of ductile iron.
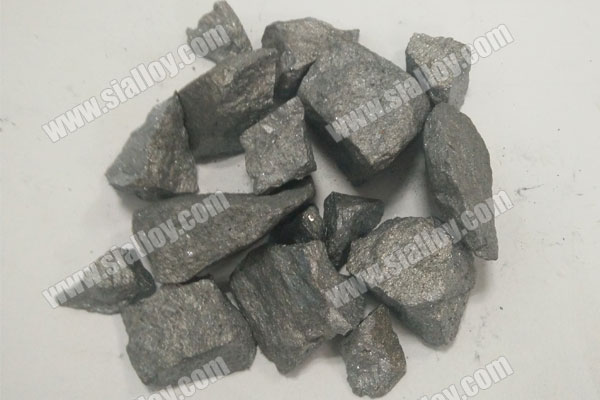
The structure and performance of ductile iron depend on the composition and crystallization conditions of the cast iron and the quality of the spheroidizing agent used. The study believes that in order to ensure the mechanical properties of ductile iron, the specific wall thickness, pouring temperature, spheroidizing agent used, and spheroidizing treatment of the casting must be considered. The optimization of process and cooling parameters and effective slag discharge measures are strictly controlled, and appropriate reduction of carbon equivalent, alloying and heat treatment are effective measures to improve ductile iron.
The main factors that control the matrix of ductile iron are the composition of the cast iron, the type of spheroidizing agent and inoculant used, the method of adding, and the cooling conditions.
1.Composition control of as-cast ferritic ductile iron
Slightly hypereutectic composition, in which carbon is slightly higher, but no graphite floats, and the silicon content is slightly lower. The silicon content of the inoculant should be less than 3%. The lower the manganese, the better. The Mn should be less than 0.4%, and the sulfur and phosphorus should be low. , Make S≤0.02%, P≤0.02%, this is because silicon can improve ductile iron structure and corresponding plasticity, Si=3.0~3.5% can get all ferrite structure. Studies have pointed out that when Si=2.6~2.8%, cast iron has the highest elongation and impact toughness, but the micro segregation of silicon in iron increases with the increase of the phosphorus content, the more serious this segregation is, and the impact on mechanical properties The adverse effect, especially when the temperature is below zero, is greater, and when the sulfur content is low, low-magnesium and low-rare earth spheroidizing agents can be used to spheroidize, and reduce the generation of "black spots" defects, and the "black spots" are mainly magnesium, Aggregate of cerium sulfide and oxide, in addition, low-silicon spheroidizing agent should be used to ensure multiple inoculations.
2.Rare earth can promote the spheroidization effect of magnesium alloy (spheroidization rate and roundness of the ball). It pays attention to the effect of preventing the distortion of spheroidal graphite in the wall thickness ductile iron. This is also the domestic and foreign spheroidizing agents that contain rare earths. One of the main reasons.
According to the classification of production methods, nodulizers can be divided into the following types:
(1) Type of spheroidizing agent