solid cored silicon calcium wire for converter
When refining in the furnace, solid-core pure calcium wire is generally used instead of solid-core silicon-calcium wire. Why? Why should such a substitution be made? Let's take a closer look at the processing flow.
The solid-core pure calcium wire reacts more intensely with molten steel than the silicon-calcium wire during the calcium treatment. It is necessary to pay attention to the calcium treatment operation, such as the feeding depth and feeding speed. During the feeding operation, the solid-core pure calcium cable has a high calcium vapor pressure. To prevent the natural evaporation of calcium, the solid-core pure calcium cable must be fed deep.
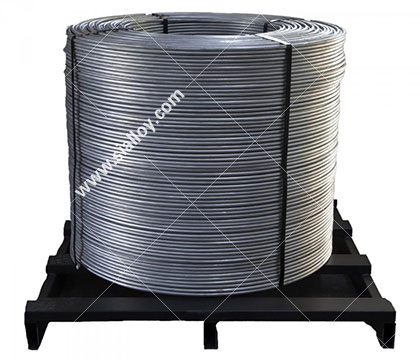
One method is to increase the thickness of the iron sheet to prevent its premature melting from affecting the calcium release depth;
Another method is to increase the feeding speed to increase the calcium release depth. The higher feeding speed enables the solid pure calcium wire to penetrate the slag layer and reach a certain depth, reduce the oxidation of Ca by the slag, and increase the effect of molten steel. The absorption of calcium improves the recovery rate of calcium.
Wire feeding speed and wire feeding rhythm are the key parameters of the solid-core pure calcium wire feeding process. Too fast or too slow wire feeding speed and rhythm will affect the melting time and oxidation degree of the solid pure calcium wire, which will affect the metallurgical effect. .
Operators must strictly pay attention to the molten steel. Once the molten steel rolls violently, they must pause for a while before continuing to feed the wire to prevent splashing.
The calcium processing mechanism of the silicon-calcium wire is the same, but the degree of chemical reaction is not so strong, so the operation of feeding the silicon-calcium wire is relatively easy. The silicon-calcium wire must choose a product with good performance to ensure the quality of use.