silicon carbide metallurgy
Silicon Carbide, usually SiC for short, contains about 70% silicon and 30% carbon. with small quantity of free carbon and free silicon. The purity can be as high as above 96%, mostly this high purity silicon carbide are used as abrasives. It includes two colors: Black SiC and Green SiC. Common metallurgical silicon carbide are with purity below 80%, in the majority of cases, it’s black color. Silicon carbide metallurgy, which mainly refers to casting usage SiC, best purity around 90%. It’s with high purity, high harness and high melting point. Lower grade silicon carbide metallurgy contains too much impurities. There also is another kind off silicon carbide metallurgy which is recycled silicon carbide. It is made from used electronic parts, so the price is cheaper.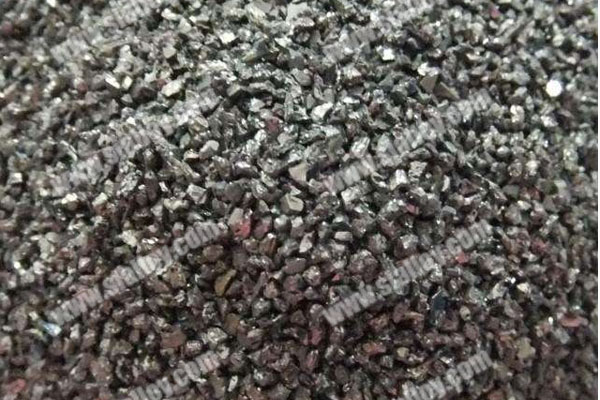
When using in electric furnace, the size of silicon carbide metallurgy shall be 0.5-3mm, for easy to melt and absorb. When using in copula furnace, the size of SiC metallurgy shall be bigger to avoid efflation by blast air. In high temperature, silicon carbide metallurgy grade will decompose into carbon and silicon ions, they will react with oxygen, then into the liquid iron respectively, and form the core of graphite. As we all know, silicon and carbon have strong inoculation ability, it will help to make cast iron. The adding amount of SiC metallurgy is 0.5-5.0%. For years people are using silicon carbide metallurgy in production of casting, and had very effective result and experience.
According to current experience, the most commom grades are silicon carbide 88 and 90%, adding amount 2.5%. Because the melting point of silicon carbide is as high as 2700℃, so the melting process is longer, we need to add it before other alloys and additives, usually it is added at whole casting procedure’s one third time to half time, so as to let it have enough time for melting and reaction. In all, silicon carbide metallurgy can replace ferrosilicon and increase the number of graphite, and enhance mechanical properties of the casting.