shrinkage cavity and shrinkage porosity
Shrinkage cavity are large and concentrated cavity that can be clearly seen, while shrinkage porosity is small and scatted cavity that are unclear. Shrinkage cavity and shrinkage porosity are more common in ductile cast iron than in gray cast iron, in order to prevent them, more attention and control much be given. In most cased, shrinkage cavity are generated at the upper part of the hot joint of the casting; there are often scatted shrinkage porosity at the hot joint of the casting and below the shrinkage cavity. However, for some centers with uniform wall thickness, or in the thick wall shrinkage porosity may also appear in the center.
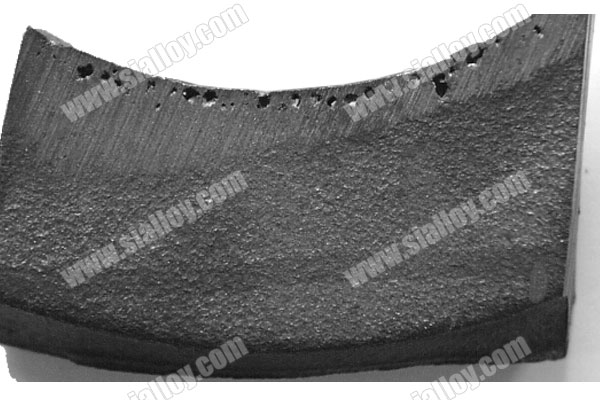
The shrinkage hole and shrinkage porosity volume of ductile cast iron are larger than gray cast iron, however, in production, the no-riser process can also be used to obtain sound ductile iron castings, the reasons for shrinkage cavity and shrinkage porosity of ductile iron are as follows:
1.Spherical graphite precipitates in molten iron After spheroidizing treatment, spheroidal graphite will precipitate in molten iron immediately, and as the temperature gradually decreases, the graphite balls in the molten iron gradually grow up. The process of graphite precipitation and growth is accompanied by the expansion of liquid metal.
2.Divorced eutectic transformation nodular cast iron undergoes eutectic transformation in a divorced eutectic way. The coagulation method is porridge-like coagulation that is almost simultaneous inside and outside, so it is easy to form microscopic shrinkage.
3.The eutectic expansion is large. Due to the porridge solidification, the casting will last a long time during the eutectic transformation. The eutectic time of ductile iron can be more than doubled than that of ordinary gray cast iron, which leads to the eutectic transformation. The graphitization expansion is large.
There are also other influence factors, such as spheroidizing treatment increases the subcooling of molten iron etc.
So what are the measures to prevent shrinkage cavity and shrinkage porosity?
1.The iron composition content of carbon, silicon, manganese, RE and magnesium must be appropriate. High carbon content can reduce the tendency of shrinkage cavity and shrinkage porosity.For thin-walled castings, when the carbon and silicon content is low, free carbides are easily produced,for thick-walled castings, lower carbon content can be used, and silicon content should be appropriately increased. Manganese is easy to form carbides and easily promotes the formation of shrinkage cavities and shrinkage porosity. For this reason, efforts should be made to reduce the manganese content, especially for as-cast ferritic ductile iron. Under the premise of ensuring spheroidization, the residual amount of magnesium and rare earths should not be too high.
2.The state of molten iron. The tendency of shrinkage cavities and shrinkage porosity is small. The slope of the cooling curve of the molten iron should be small and the degree of subcooling should be small. The expansion of the eutectic during solidification is small, and the secondary shrinkage is also small. The conditions to be met are: (1) slow cooling rate (2) high carbon equivalent and high tendency to precipitate graphite. (3) There are many effective graphite cores in molten iron. (4) Good gestation effect.
3.Casting temperature in order to prevent shrinkage cavities and shrinkage porosity, it is necessary to reduce the amount of liquid shrinkage, and low casting temperature is advantageous. However, for thin-walled (10mm) castings, carbides are prone to appear. At this time, it is difficult to use the feeder to feed. Therefore, the appropriate pouring temperature also depends on the structure and wall thickness of the casting.
4.The gating system adopts a sequential solidification method, which can effectively prevent the design and placement of castings, risers, riser necks, internal runners and runners, as well as the setting of external cooling iron and the use of metal molds when necessary. Effective measures for shrinkage and porosity.
Anyang Huatuo Metallurgy in the raw materials such as silicon, manganese, carbon for cast iron industry for more than 10 years, own rich experience in the cast iron production, if you need, we want to share more experience of the cast iron to you.