role of alloying elements in casting
In order to improve and enhance certain properties of steel, the elements that are intentionally added during the smelting process are called alloying elements.Commonly used alloying elements are chromium, silicon, manganese, rare earth and nickel, molybdenum, tungsten, vanadium, titanium, niobium, zirconium, cobalt aluminum, copper, boron and so on. Phosphorus, sulfur, nitrogen, etc. also function as alloys in some cases.
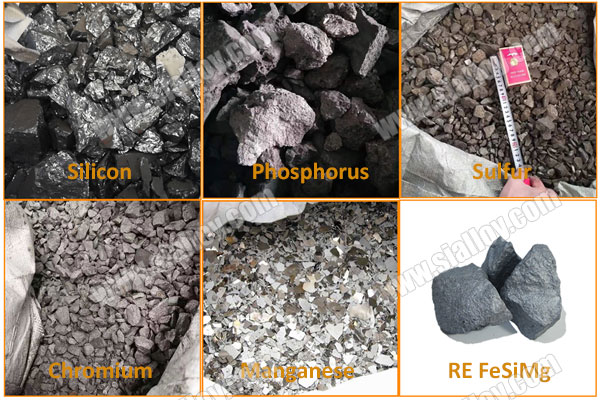
Chromium:The main function of chromium in the quenched and tempered structure is to improve the harden-ability, chromium-containing carbides can also be formed in the carburized steel, thereby improving the material wear resistance of the surface, in electric heating alloys, chromium can improve the oxidation resistance, electrical resistance and strength of the alloy. When the content of chromium exceeds 12%, the steel has good high temperature oxidation resistance and oxidation corrosion resistance, and also increases the thermal strength of the steel. When the chromium content exceeds 15%, the strength and hardness will decrease, and the elongation and reduction of area will increase accordingly. Chromium-containing steel parts can easily obtain higher surface finish quality after grinding.
Silicon can reduce the density, thermal conductivity and electrical conductivity of steel. It can promote the coarsening of ferrite grains and reduce the coercivity. It has a tendency to reduce the anisotropy of the crystal, which makes the magnetization easier and the magnetic resistance is reduced. It can be used to produce electrical steel, so the magnetic resistance loss of the silicon steel sheet is low. Silicon can increase the magnetic permeability of ferrite, so that the steel sheet has a higher magnetic induction intensity under a weaker magnetic field. However, silicon reduces the magnetic induction intensity of steel under a strong magnetic field. Silicon has a strong deoxidizing power, thereby reducing the magnetic aging effect of iron. When silicon-containing steel is heated in an oxidizing atmosphere, a layer of SiO2 film will be formed on the surface, thereby improving the oxidation resistance of the steel at high temperatures. Silicon can promote the growth of columnar crystals in cast steel and reduce plasticity. If silicon steel cools faster when heated, due to its low thermal conductivity, the temperature difference between the inside and outside of the steel is large, and it will break. Silicon can reduce the welding performance of steel. Because silicon has a stronger bond with oxygen than iron, it is easy to generate low-melting silicate during welding, increase the fluidity of slag and molten metal, cause splashing, and affect welding quality. Silicon is a good deoxidizer. When using aluminum to deoxidize, add a certain amount of silicon as appropriate, which can significantly improve the rate of deoxidation.
Manganese:Good deoxidizer and desulfurizer. Steel generally contains a certain amount of manganese, which can eliminate or weaken the hot brittleness of steel caused by sulfur, thereby improving the hot workability of steel. The solid solution formed by manganese and iron improves the hardness and strength of ferrite and austenite in steel; at the same time, it is an element formed by carbides, which enters the cementite to replace part of the iron atoms. Manganese in steel reduces the critical transformation temperature. It plays the role of refining pearlite and indirectly improves the strength of pearlite steel.
RE: It can improve the plasticity and impact toughness of forged and rolled steel, especially in cast steel, it can improve the creep resistance of heat-resistant steel electric heating alloys and superalloys. RE can also improve the oxidation resistance and corrosion resistance of steel, it can also improve the fluidity of steel, reduce non-metallic inclusions, and make the steel structure dense and pure.
Sulfur: Increasing the content of sulfur and manganese can improve the cutting performance of steel, in free-cutting steel, sulfur is added as a beneficial element, however, the severe segregation of sulfur in the steel will deteriorate the quality of the steel. At high temperatures, the plasticity of the steel will be reduced, and it is generally controlled at 0.02% to 0.05%.
Phosphorus: It plays a strong role in solid solution strengthening and cold work hardening in steel. As an alloying element added to low-alloy structural steel, it can improve its strength and atmospheric corrosion resistance, but reduce its cold stamping performance. Phosphorus is used in combination with sulfur and manganese to increase the cutting performance of steel and increase the surface quality of processed parts. It is used for free-cutting steel, so free-cutting steel has a relatively high phosphorus content. However, the serious segregation of phosphorus will increase temper brittleness and make the steel easy to be brittle during cold working, so the general content is not more than 0.03% to 0.04%.
Of course, nickel, molybdenum, tungsten, vanadium, titanium, niobium, zirconium, cobalt-aluminum, copper and boron all have certain effects on the wear resistance and machinability, hardness, corrosion resistance, hardenability and thermal strength of steel.
Anyang Huatuo Metallurgy has been engaged in casting materials for more than 10 years, which has advanced equipment and employees have been professionally trained to provide raw materials such as ferro silicon, manganese metal, ferro phosphorus and pyrite, it always adhere to the principle of quality first, customer first, believe that can help you produce better quality castings.