requirement of ferrous oxide content and basicity of oxidizing slag
The requirements for oxidizing slag in the steelmaking process are: higher alkalinity, stronger oxidizability, appropriate amount of slag, good fluidity and proper foaming.Alkalinity is a measure of acidity and alkalinity of slag and is a necessary condition for effective dephosphorization in the steelmaking process. The simple and commonly used method for expressing alkalinity is the ratio of CaO content in slag to SiO2 content, namely w (CaO) / w (SiO2). Theoretical research shows that under the same ΣFeO content in Slag, the activity is the largest when the alkalinity is 1.87, and the slag is the most oxidizable. In actual production, it is based on this theory and the specific process to control the acidity and alkalinity of slag. Oxidation top-blown converter steelmaking usually controls the alkalinity in the range of 2.4-2.8; for the case where the raw material contains high phosphorus or smelting low-sulfur steel, the alkalinity is controlled above 3.0. During the melting period of EAF steelmaking, the basicity of the slag is generally controlled at about 2.0; after entering the oxidation period, as the temperature increases, the alkalinity gradually increases to 2.5-3.0; and the decarburization is used in the middle and later stages of oxidation Mainly, the alkalinity is usually reduced to about 2.0.
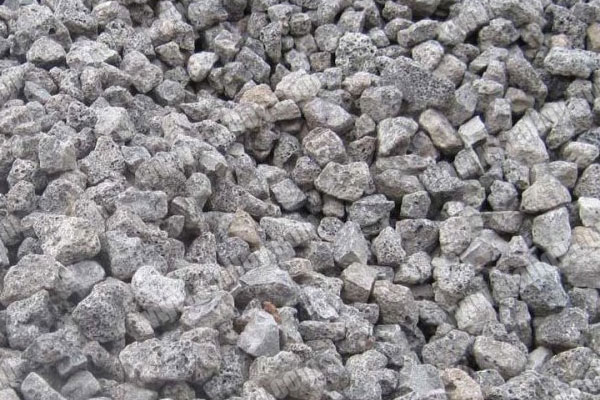
The level of ΣFeO in Slag indicates the strength of slag oxidizing and dephosphorization ability. When the alkalinity is fixed, the oxidizing property of the slag increases with the increase of ΣFeO content in the slag. However, too high ΣFeO also has some side effects, so its content is generally controlled between 10% -20%. In the oxygen top-blown converter steelmaking, the w (ΣFeO) is sometimes as high as 30%, but the w (ΣFeO) in the final slag is required to be as low as possible.