recarburizers in steel making
Customer Q: Hello! Our company has recently purchased a batch of recarburizers. During the use process, the absorption rate of recarburizers has not reached the standard. How can I increase the absorption rate when using those few?
Customer Service Answer: Hello customers, recarburizers have always been the iron alloy products that steelmakers often purchase. There are often various problems in the use. For the increase of the absorption rate, we provide you with three use cases. The points of attention can help you solve the problem of the absorption rate of the recarburizer!
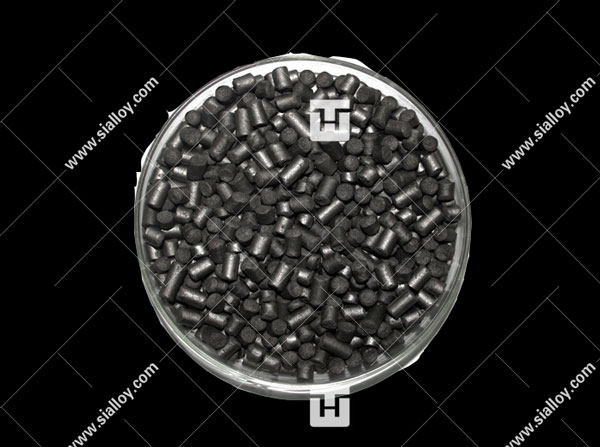
It is better to choose a carbonaceous agent with moderate particle size and high density when selecting a carbonizer. Because the denser the carbonizing agent, the larger the particle size, the less easy to absorb. Compared with the power frequency furnace, the intermediate frequency furnace heats up too fast, and the absorption rate of the petroleum coke recarburizer in the intermediate frequency furnace is lower, in order to achieve the recarburizing agent. Higher absorption rate, avoiding long-term high temperature oxidation of the recarburizer, the power in the early stage should be small enough to prolong the heating time of the graphitized recarburizer to increase the absorption rate.
The efficiency is further improved by mechanical agitation and, if necessary, manual mixing. Because the mixing ability of the intermediate frequency furnace is poor, it should also assist the appropriate manual mixing. For example, the medium-transfer iron is used to promote the dissolution and diffusion of the recarburizer, and the absorption rate is increased. The specific gravity of the recarburizer is small, and the artificial agitation can reduce the recarburizer floating on the surface. When it is burnt, the stirring can also reduce the carbonation holding time and shorten the production cycle. However, if the stirring time is too long, the recarburizer will be burned seriously, so the proper feeding process and melting power also play an important role in the absorption of the recarburizer.
A reasonable method of joining cannot be blindly added at one time. In order to avoid slow smelting and heating time, in the batching process, scrap steel and recarburizer are added in batches. The melting time of each batch is about 15 minutes. In the early stage of the chemical, lower power is used to avoid excessive temperature and the recarburizer is burned. Loss, after the expectation of molten iron paste, quickly heat up. For example, a total of 130KG of recarburizing agent needs to be added, and 60KG+40KG+30KG is added to avoid the large-scale addition of the recarburizing agent suspended on the surface of the molten iron, which cannot be combined with the molten iron and the temperature is too high. The burning loss is serious, and the amount of the last addition should be relatively small, avoiding the addition of a recarburizing agent to the molten iron in large quantities, resulting in incomplete absorption of the graphite recarburizer in the molten iron and delay in production.