interfering elements in casting
There are three sources of interfering elements in casting:
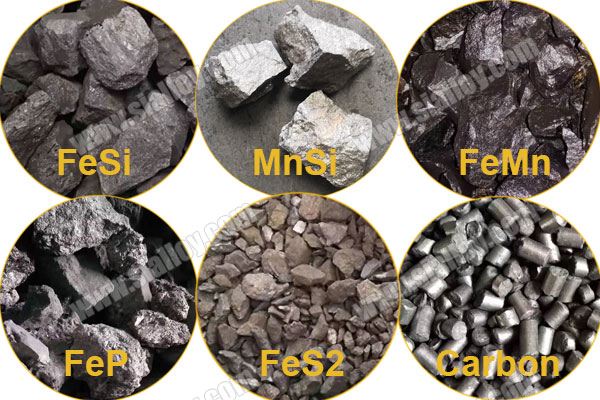
1.The harmful elements usually contained in steel, steel castings and iron castings, such as sulfur, phosphorus (sometimes a small amount of phosphorus is deliberately added to some wear-resistant cast iron), lead (sometimes a small amount of lead is added to free cutting steel), etc.
2.Alloying elements specially added to improve the properties of steel, such as manganese, chromium, molybdenum, titanium, vanadium, niobium, boron, etc.
3.The pollutants mixed in the charge.
Harmful elements such as phosphorus, sulfur and other interfering elements contained in pig iron for steelmaking can be removed in the subsequent steelmaking process, while cast iron is only directly made into castings after remelting, and various harmful elements and A considerable part of the interfering elements still remains, and if the content exceeds the allowable value, it will affect the performance of the material. When manufacturing high-quality iron castings, the content of harmful elements and interfering elements in raw pig iron must be strictly controlled.
When smelting cast iron with an induction furnace, the amount of cast iron ingots in the charge is very small, and the share of scrap steel increases, while the alloying elements in the steel have a negative impact on the performance of cast iron (especially ductile iron), and even become pollution. element. On the other hand, low-boiling elements that are easy to remove in the cupola smelting process, such as Pb (1755°C), Sb (1640°C), Bi (1481°C), Te (989.8°C), As (615°C sublimation), Cd (767°C), Zn (419.5°C), etc., are more difficult to remove when smelted in an induction furnace, so it is easy to show their negative effects. In addition, due to the huge increase in the demand for scrap steel, its sources involve all walks of life, and it is inevitable to mix some polluting elements, such as lead, aluminum, zinc, etc.
Effects of interfering elements on the properties of cast iron:
1.Form carbides.
Alloying elements in steel, such as Mn, Cr, V, Mo, Ti, B, etc., are strong carbide-forming elements, and are easy to segregate in the final solidified part of the casting, with a high concentration at the grain boundary. For gray cast iron, due to the existence of a large number of flake graphite in its structure, the strength is not high, the ductility and toughness are very poor, and the effect of carbides at the grain boundaries is not so obvious. For ductile iron, especially ferritic ductile iron, austempered ductile iron and high-quality thick-section ductile iron, the effect of carbides at grain boundaries is often crucial.
2.Influence on graphite spheroidization.
Graphite can be spheroidized by adding Mg and rare earth elements represented by Ce into cast iron. If the metal charge contains elements that hinder the spheroidization of graphite, it will affect the spheroidization of graphite.
The effect of hindering graphite spheroidization can be roughly divided into two aspects:
(1)Reaction with Mg or rare earth elements to produce oxides, sulfides and nitrides, consuming spheroidizing elements. It is mainly oxygen, sulfur and nitrogen that play this role. In addition, tellurium (Te) and selenium (Se) are also elements that consume spheroidizers.
(2)After the nodular graphite is formed, the stability of the liquid phase in the cast iron is improved, so that the graphite grows unevenly in all directions during the growth process, resulting in the distortion of the graphite ball. The main elements that play this role are phosphorus, aluminum, tin, copper, boron, antimony, titanium, and niobium. These elements have a strong tendency to segregate, which can stabilize the liquid phase in iron and promote the anisotropy of graphite growth, thereby affecting the shape of graphite.
3.The tendency to generate shrinkage cavities increases.
Shrinkage cavities are characterized by surface shrinkage cavities and internal shrinkage cavities and shrinkage porosity. When the content of titanium and aluminum increases, the fluidity of molten iron deteriorates, and the tendency to produce surface shrinkage cavities increases. Phosphorus, manganese, chromium, vanadium, molybdenum and other elements are easy to segregate in the final solidified part to form composite carbides, resulting in an increased tendency to generate internal shrinkage cavities and shrinkage porosity. Studies have shown that gray cast iron contains elements such as aluminum, titanium, vanadium, chromium, and phosphorus, and the tendency to generate shrinkage cavities increases; in ductile iron, the aluminum content increases from 0.02% to 0.4%, and the tendency to generate shrinkage cavities increases.
4.The strength of gray cast iron is reduced.
The morphology of graphite (type A, type B, type C, type D or type E) in gray cast iron structure has an important influence on its mechanical properties, and its strength is difficult to predict from hardness. If the lead content in gray cast iron is above 0.005%, Widmanite graphite may be produced, resulting in a significant reduction in strength. If the cast iron also contains aluminum, hydrogen, calcium and other elements, and the lead content is below 0.005%, Widmandarin graphite may appear.
5.The hardness of cast iron is low.
Studies in the United States have shown that the boron content in cast iron exceeds 0.002%, which can inhibit the effect of copper stabilizing pearlite and reduce the hardness of cast iron. Therefore, not only should we pay attention to the boron contained in scrap steel and other furnace materials in production, but also pay attention to the pollution caused by boric acid added to the furnace building materials when using induction furnace for smelting.
6.The service life of the induction furnace lining is low.
In recent years, the number of induction furnaces used for smelting cast iron has been increasing, and the life of the furnace lining is not long. The problems caused by the charge cannot be ignored. If the galvanized steel sheet is used as the charge, the zinc will evaporate after being heated and penetrate into the furnace lining, which will reduce the service life of the charge. During the sintering of newly built furnace linings, the effect of zinc vapour is particularly serious.
Anyang Huatuo Metallurgy Co., Ltd in qualified ferroalloys for steel-making and casting for more than 10 years, can supply the ferro silicon, silico manganese, ferro manganese, etc, welcome for your consult.