influence of major elements on graphitization of cast iron
The five major elements in cast iron are carbon, silicon, manganese, sulfur, and phosphorus. Carbon and silicon are the two most important chemical elements in ordinary gray cast iron,they have a decisive influence on the structure and properties of cast iron,during production, the structure and performance of ordinary gray cast iron are often controlled and adjusted by controlling and adjusting the content of carbon and silicon.
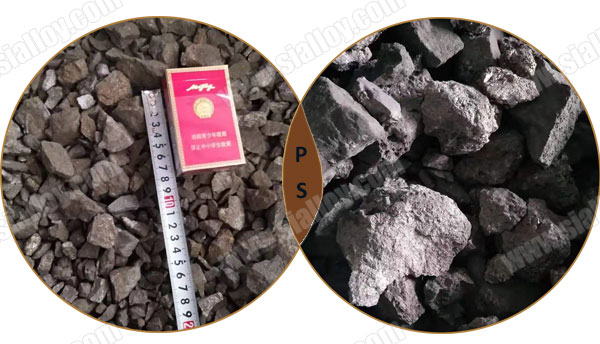
Carbon itself is an element that constitutes graphite, increasing the carbon content can increase the homogeneous nuclei of graphite,and also increase the undissolved graphite inclusions in the molten iron and increase the heterogeneous nuclei of graphite,which can increase the actual crystallization temperature of molten iron.However, if the carbon content too high will increase the degree of graphitization of the cast iron ,the graphite will be coarser, the spheroid in the matrix will decrease, and the ferrite will increase, which will reduce the mechanical properties of the casting.In order to improve the strength of cast iron, refine the graphite in the structure, reduce the graphite amount, and increase the pearlite, it is necessary to appropriately reduce the carbon content in the cast iron.
Silicon is an element that strongly promotes graphitization. Increasing the silicon content can increase the degree of graphitization of cast iron, increase the amount of ferrite in the matrix structure and decrease the amount of pearlite.If the silicon content too low will make the graphitization not good, then tingling or white mouth tissue will easily appear. However, if the silicon content too high will make the graphite coarsened and the mechanical properties reduced. In the order of adding the charge, the process requirements of adding manganese first, then carbon, and then silicon must be strictly observed. If there is no need to add manganese to cast iron, follow the principle of adding carbon first, then silicon. Because silicon and sulfur have an effect on the absorption of recarburizer.
Manganese is an element that hinders graphitization, which increases the amount of pearlite in the cast iron matrix and obtains refined pearlite.When it is necessary to ensure the pearlite of cast iron, the manganese content is usually controlled in the range of 0.6%-1.2%. If the manganese content is too high, free cementite will appear in the cast iron structure, showing a tendency of white mouth.Manganese can be dissolved in ferrite to form a replacement solid solution, and it can also be dissolved in cementite to form manganese-containing cementite. The dissolution of manganese in cementite will strengthen the binding capacity of iron and carbon, making the cementite more stable, thus hindering graphitization. The influence of manganese on graphitization can only be manifested through the remaining part after it chemically reacts with sulfur.
Sulfur is a harmful element in cast iron. It is completely dissolved in molten iron in the form of iron sulfide and can reduce the solubility of carbon in iron (1% of sulfur can reduce about 0.5% of carbon), but when the cast iron is solidified, The solubility of sulfur in solid solution (austenite and ferrite) or cementite is very small. When the sulfur content in the molten iron is about 0.02%, it can form an independent sulfide phase. Its composition, nature and existence form are determined by It is determined by the content of manganese and other elements in cast iron. In addition, sulfur deteriorates the casting performance of cast iron in cast iron. When there is a large amount of sulfide in the molten iron, the fluidity of the molten iron will decrease, resulting in poor feeding performance and easy to produce defects such as cracks. Therefore, the sulfur content in gray cast iron is generally limited to 0.1-0.12% or less.
Phosphorus has little effect on the graphitization of cast iron. Phosphorus same like silicon can move the eutectic point of cast iron to the left. When the phosphorus content in the molten iron reaches 1%, the carbon content of the eutectic point can be reduced by 0.3% in the molten iron. But in contrast to silicon, phosphorus lowers the eutectic transition temperature. Phosphorus can be completely dissolved in molten iron, but the solubility is very small in the solid state, and decreases with the increase of carbon content in cast iron (for example, 1.2% phosphorus can be dissolved in pure iron, while the carbon content is 3.5 % Of cast iron can only dissolve 0.3% of ash). At the same time, the diffusion rate of phosphorus in the solid iron is slow, and it is easy to segregate during the solidification process and concentrate more in the remaining liquid, thereby forming a low melting point phosphorus eutectic. In production practice, it was also found that when the phosphorus content of cast iron is high, the tendency of castings to produce defects such as sand sticking and pores is significantly reduced.
There are exiting the materials such as recarburizer (CPC,GPC etc),ferro silicon, ferro manganese and ferro silico manganese,ferro phosphorus, pyrite(FeS2) which can adjust the content of carbon, silicon, manganese, phosphorus and sulfur, Anyang Huatuo Metallurgy Co.,Ltd in such materials for more than 10 years, if any need, welcome for consult.