how to use recarburizer in electric furnace casting
The electric furnace is a relatively wide range of industrial equipment in the foundry. It can be said that the foundry's production of castings depends entirely on the electric furnace. We have also talked about the application of the recarburizer before casting. The role of casting can be described as a compliment, and what we are talking about today is the question of how to use recarbonizer in electric furnace casting. For this reason, we specifically consulted the casting master to tell you the correct method!
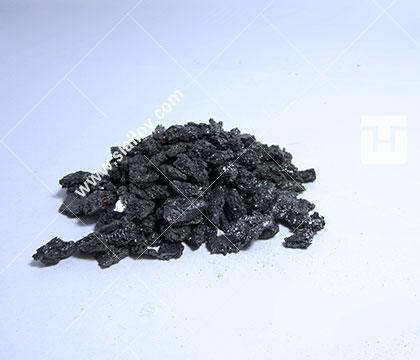
First of all, the correct method of using a recarburizer for a medium-frequency induction furnace with a weight of 3 tons. When using this furnace, the teacher suggested that we should fine-tune the recarburizer. The reason is that the furnace is single and stable. When melting or a small amount of molten iron is left in the furnace, add the recarburizing agent to be added to the surface of the plaster at once, and immediately add the metal charge to press all the recarburizing agent into the molten iron to make the recarburizing agent and molten iron fully Contact, the absorption rate is above 90%.
Many small foundries also have many small medium-frequency electric furnaces. When using this kind of electric furnace with a recarburizing agent, it is also necessary to fine-tune the recarburizing agent, but the raw material of this electric furnace is sandwiched with high-carbon materials such as pig iron. After adjusting the carbon content in the molten iron, the teacher told us that it is usually necessary to add it on the surface of the molten iron. The vortex stirring of the molten iron through the electric furnace and the manual stirring of the product will dissolve and absorb this product. The carbon absorption rate is about 93%.
Heavy-duty electric furnaces are generally more than 5 tons, and the feeding is generally single. The teacher told us that when using such an electric furnace for charging, the recarburizing agent generally adopts the dispersed addition method. According to the requirements of carbon content, according to the proportion of ingredients, it will increase The carbon agent and the metal charge are added to the middle and lower parts of the electric furnace together with each batch. One layer of metal charge and one layer of recarburizer. The carbon absorption rate can reach 90% -95%. Don't slag when the recarburizer is melted, otherwise it will be easy Wrapped in waste residue, affecting carbon absorption.
The teacher told us the correct use method of the recarburizer, we can choose different recarburizer use methods according to different electric furnace casting, so that it can effectively improve the absorption rate of the recarburizer, improve the process quality, and save the recarburizer Casting consumes, so it is important to use recarburizer in electric furnace casting!