how to prevent the bright carbon slag inclusions in casting
Bright carbon forms a deposited film on the surface of the sand mold on the melt surface. The relatively thick bright carbon film layer, especially on the surface of the sand core, is mainly due to the gas pressure generated by the pyrolysis of the resin. Flow marks formed by the separation of slag inclusions and metal by non-wetting membranes are difficult to detect, mainly because they often appear on vertical walls of castings or are overlapped.
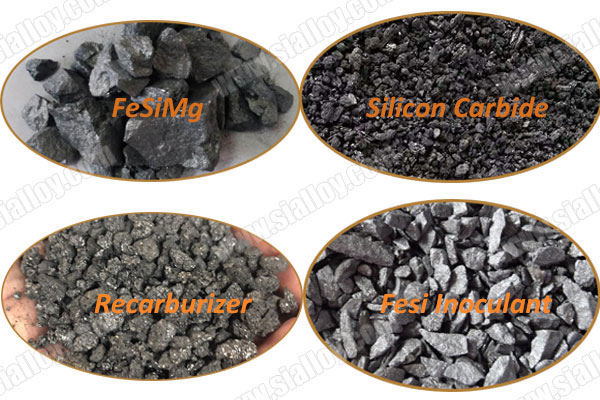
Bright carbon slag inclusions mainly occur in molding sands and core sands where bright carbon is excessively formed, and they are usually deposited in areas with large fluctuations in casting density differences. As for ductile iron, they are more frequently present with oxide slag inclusion defects.
Causes of bright carbon slag inclusions:
1.Resin sand: The amount of bright carbon produced by the core sand binder is too high; other others because of insufficient core exhaust.
2.Clay sand: Excessive bright carbon formation in modeling sand; Carbon supports produce too much or rapidly release bright carbon.
3.Modeling: The air permeability of the molding sand surface is too low.
4.Pouring: Excessive turbulence, resulting in bright carbon slag inclusions; Pouring temperature too low;The different thermal expansion coefficients of silica sand and bright carbon deposits can also promote the separation of thicker bright carbon films.
How to prevent bright carbon slag inclusion defects in castings.
1.Resin sand: Reduce the core sand binder content and, if necessary, replace with a low gloss carbon producing binder; Preheat sand cores before use to reduce the proportion of solvent contained; Improve the exhaust capacity of the core sand, check the filler residue in the core head, and choose coarse sand; Add an oxidant to the core sand; Apply a thicker coat of paint to the sand core.
2.Clay sand: Reduce bright carbon production in molding sand by reducing the amount of additives added or selecting other carbon materials with low bright carbon production and slower gas release capabilities;Improve breathability of styling materials.
3.Modeling: Reduce the compaction pressure on the molding machine; Improve the air permeability of the sand mold.
4.Pouring: Avoid turbulence, ensure laminar pouring, and add filters if necessary; Increase the pouring temperature.
There are also other aspects need to pay attention for casting such as qualified raw materials added like FeSi/BaSi inoculant, FeSiMg spheroidizing agent, carbon, etc, Anyang Huatuo professional in raw materials for steelmaking and casting for more than 15 years, so just trust us provide you the best service.