graphite floating of ductile cast iron
Several days ago, shared the problem of slag inclusion and shrinkage of ductile cast iron, today will share other problem graphite floating of ductile cast iron, in order to produce high quality ductile cast iron, the graphite floating problem is also need to pay more attention.
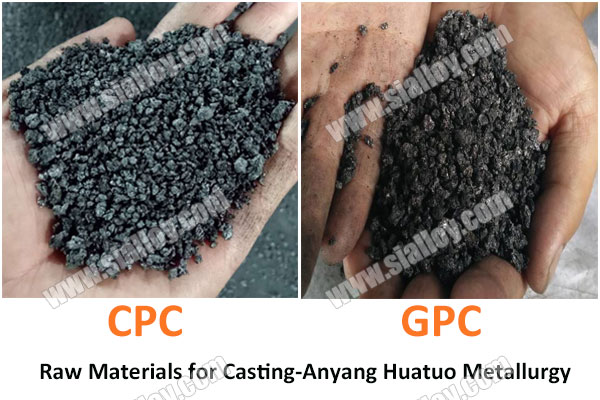
Influencing factors of graphite floating:
(1)Carbon equivalent: The carbon equivalent is too high, so that a large amount of graphite is precipitated in the molten iron at high temperature. Because the density of graphite is lower than that of molten iron, the graphite floats to the upper part of the casting under the drive of magnesium vapor. The higher the carbon equivalent, the more serious the graphite floating phenomenon. It should be pointed out that too high carbon equivalent is the main reason for graphite floating, but it is not the only reason. Casting size and wall thickness are also important factors affecting graphite floating.
(2)Silicon: Under the condition of constant carbon equivalent, appropriately reducing the silicon content will help reduce the tendency of graphite to float.
(3)RE: When the content of RE is too small, the solubility of carbon in molten iron will decrease, and a large amount of graphite will be precipitated out of molten iron, which will aggravate graphite floating.
(4)Spheroidizing temperature and inoculation temperature: In order to improve the absorption rate of magnesium and rare earth elements, domestic experimental studies have shown that the most appropriate molten iron temperature during spheroidizing is 1380~1450℃. In this temperature range, as the temperature increases, the absorption rate of magnesium and rare earths increases.
(5)Pouring temperature: In general, the higher the pouring temperature, the greater the tendency for graphite to float. This is because the casting is in the liquid state for a long time to facilitate the precipitation of graphite. A.P.Druschitz and W.W.Chaput found that if the solidification time is shortened, as the pouring temperature increases, the tendency of graphite to float decreases.
(6)Residence time: The residence time between the incubation treatment and the completion of pouring is too long, which provides conditions for the precipitation of graphite. Generally, this time should be controlled within 10min.
Anyang Huatuo commitment to the production and sales of casting materials long-term, own rich experience in the production and export of recarburizer, spheroidizing agent and inoculant for casting/foundry, so if you have any confused, please contact us, we will try to help.