RE magnesium ferrosilicon spheroidizing agent
Spheroidizing agent is currently one of the main methods for obtaining ductile iron. According to the production method, it is divided into magneisum-silicon alloy, RE magnesium ferrosilicon alloy, calcium-based alloy (mostly used in Japan), nickel-magnesium alloy, pure magnesium alloy, RE alloys, the most widely used in the world is RE magnesium ferro silicon alloy.
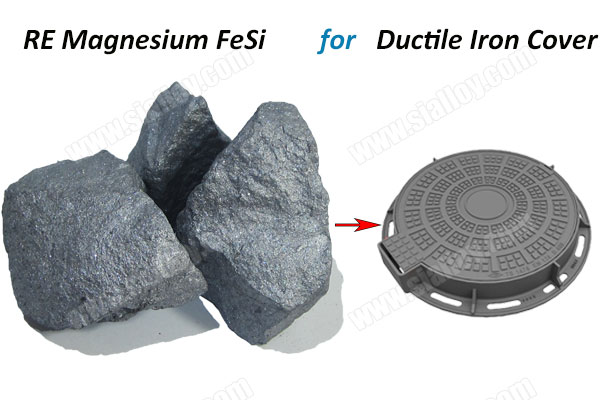
RE magnesium ferro silicon alloy is an alloy melting made of ferrosilicon, calcium, magnesium, RE etc. It is a good spheroidizing agent and has a strong deoxidizing and desulfurizing effect, ferrosilicon, lanthanum cerium metal or RE silicon, magnesium metal are the main raw materails. The production of RE magnesium ferrosilicon alloy is produced in a submerged arc furnace, which consumes a lot of power, and can also be produced in an intermediate frequency furnace.
Conventionally, RE magnesium ferrosilicon spheroidizing agents can be divided into low magnesium, medium magnesium and high magnesium. The magneisum content of 4%,5%,5.5% belongs to low magneisum, and the RE is between 1% and 2%, it is mostly used for smelting in intermediate frequency furnace and spheroidizing treatment of low-sulfur molten iron, it has the advantages of gentle spheroidization reaction and easy absorption of spheroidizing elements. Magnesium content of 6% and 7% belongs to the medium magnesium series spheroidizing agent, which is mostly used in cupola, electric furnace double smelting, or intermediate frequency furnace smelting pearlite cast ductile iron castings. According to the casting wall thickness and the sulfur content of the original molten iron, determine the appropriate amount of spheroidizing agent, which has a wide range of applications and a wide range of spheroidizing treatment processes. High-magnesium series spheroidizing agent is suitable for cupola smelting and molten iron with sulfur content of 0.06%-0.09%, the addition amount is between 1.6%-2.0%. The low-aluminum spheroidizing agent is used for castings that are prone to subcutaneous pore defects and castings that require aluminum content in molten iron. The spheroidizing agent produced by pure Ce and pure La has less pure inclusions and round graphite balls after spheroidization.
The more commonly used is the cored wire spheroidizing agent. The cored wire is quickly fed into the molten iron to achieve the purpose of spheroidization. This kind of spheroidizing agent is more expensive, and the equipment investment is large, but the alloy absorption rate is high during the treatment, so the treatment total cost of ductile iron has hardly increased.
There are some elements in the casting that can destroy and hinder the spheroidization of graphite. These elements are the so-called spheroidization interference elements. The interference elements are divided into two categories. One is the consumption of spheroidization element-type interference elements, which form MgS, MgO, MgSe, RE2O3, RE2S3, RE2Te3, etc., reduce the spheroidizing elements and destroy the formation of spheroidal graphite; the other is intergranular segregation interference elements, including tin, antimony, arsenic, copper, titanium, aluminum, etc. in eutectic crystallization These elements are enriched in the grain boundary and promote the formation of deformed dendritic graphite in the later stage of eutectic. The greater the atomic weight of the spheroidizing interference element, the stronger the interference effect. Many studies have now found that the interference element is in cast iron. When the content of these elements is less than the critical content, distorted graphite cannot be formed. Interfering elements have a greater destructive effect when the casting wall is thick and the cooling rate is slow. In addition, interfering elements also have an impact on the ductile iron matrix. Te and B strongly promote the formation of white mouth, and Cr, As, Sn, Sb, Pb, Bi stabilize pearlescent Al and Zr promote ferrite.
Huatuo Metallurgy has been engaged in the production and sales of spheroidizing agent for more than 10 years. It uses intermediate frequency furnace smelting to produce with small quality deviations, and has the advantages of high purity of RE and magnesium alloys, less oxidized slag, stable reactions, long spheroidizing duration, less magnesium light and less dense smoke, and the produced type is complete in varieties and specifications. Welcome to consult.