how to produce high strength gray cast iron
Electric furnace smelting high-strength gray cast iron, the following points can be ensured to ensure quality:
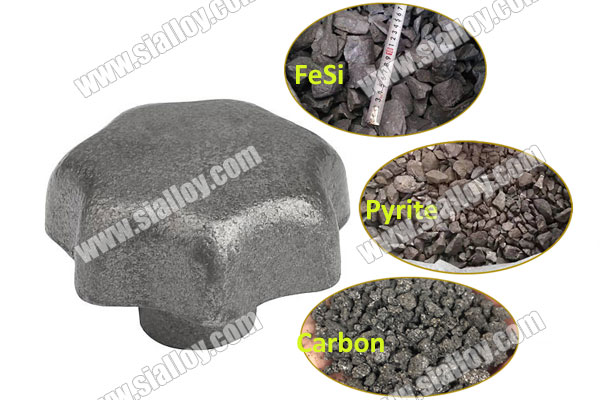
1.Design of high strength alloy gray cast iron. Adding a small amount of multi-component alloy components in cast iron, choosing reasonable process parameters, so that the casting has a certain chemical composition and cooling rate, to obtain the ideal metallographic structure and mechanical properties.Firstly,to ensure the mechanical properties, it is necessary to control the matrix structure and graphite morphology,if the carbon content is too high, the cooling rate at the thick wall of the casting is slow, and the thick wall of the casting is prone to coarse grains and loose structure, and the hydraulic test is prone to leakage;if the carbon is too low, the thin wall of the casting is likely to form hard spots or local hard zone, resulting in poor cutting performance.So control the carbon to 3.95% to 4.05% can not only ensure the mechanical properties of the material, but also beneficial to remove the blowholes and shrinkage defects of castings.Secondly,to consider the role of alloying elements,in the eutectic transformation, chromium hinders graphitization, promotes carbides, and promotes white mouth; while copper promotes graphitization and reduce cross-section white mouth. Adding appropriate amount of chromium and copper is conductive to improve the compactness of the material itself and improving its ability to resist leakage.Tin can effectively increase the content of pearlite in the matrix structure, and promote and stabilize the formation of pearlite, the pearlite-based cast iron has high strength and good wear resistance.
2.Strictly control the quality of raw and auxiliary materials. The raw and auxiliary materials entering the factory must be sampled and analyzed, unqualified raw and auxiliary materials will never be put into use. Ferro alloys and inoculants are also purchased on a fixed-point basis, striving for stable ingredients and qualified lump, sort and stack to avoid moisture.The alloy elements are based on the principle of one-time mixing, and the middle limit is used for other ingredients except silicon.The phosphorus and sulfur contents are strictly controlled. The phosphorus and sulfur contents are mainly derived from pig iron, which can be selected by the charge of phosphorus and sulfur is controlled within the required range, so the phosphorus of pig iron must be less than 0.06%, and the sulfur is less than 0.04%.All metal materials are accurately measured in strict accordance with the requirements.
3.Proper Inoculant treatment. Production practice shows that strontium, barium, calcium, ferro silicon inoculants are the most ideal inoculants for increasing strength gray cast iron, this inoculant exerts the anti-decay ability of barium and increase the share of A-type graphite, the strong strength of strontium eliminates white mouth capability, calcium and silicon assist in inoculation and penetration, the inoculant of this strength combination is an ideal choice for the inoculation of high-strength cast iron.
There are also more details need to be noticed for the production of high-strength gray cast iron, also the qualified raw materials used is also important, there will involved to the recarburizer, iron pyrite, ferro phosphorus, also the inoculant such as ferro silicon, barium silicon, rare earth ferro silicon magnesium etc, Anyang Huatuo has in such raw materials for casting for more than 10 years, always supply qualified products, adhere to customer first, quality first, if any requirement or confused, welcome for your contact or leave us your message.