processing and application of high silicon cast iron
Adding a certain amount of certain alloying elements to cast iron can obtain alloy cast iron with higher corrosion resistance in some media. High silicon cast iron is one of the most widely used. A series of alloy cast irons containing 10% to 16% silicon are called high silicon cast irons. Except for a few varieties with silicon content of 10% to 12%, the silicon content is generally 14% to 16%. When the silicon content is less than 14.5%, the mechanical properties can be improved, but the corrosion resistance is greatly reduced. If the silicon content reaches more than 18%, although the alloy is resistant to corrosion, the alloy becomes very brittle, so that it is not suitable for casting. Therefore, the most widely used industrially is high-silicon cast iron containing 14.5% to 15% silicon.
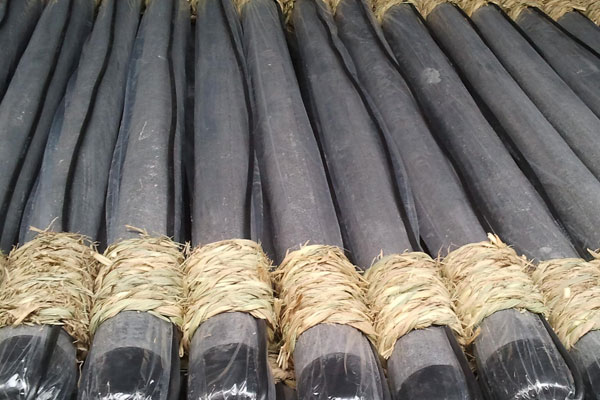
Processing
High-silicon cast iron has the advantages of high hardness and good corrosion resistance, and has been used as a material for mechanical seal friction pairs in chemical production. Because cast iron contains 14-16% silicon, has high hardness and high brittleness, there are some difficulties in manufacturing. However, through continuous practice, it has been proved that high-silicon cast iron can still be machined under certain conditions.
The high-silicon cast iron is processed on a lathe, the spindle speed is controlled at 70~80 rpm, and the tool feed is 0.01 mm. Before rough turning, the casting edges should be ground off. The feed amount of rough turning is generally 1.5-2 mm for the workpiece.
The feed direction is reversed. Because high-silicon cast iron is brittle, it feeds from the outside to the inside according to the general material, and finally the corners are broken at the edges, resulting in scrapping of the workpiece. According to practice, the reverse feed is adopted to avoid the phenomenon of broken corners and edges, and the final cutting amount of the smooth knife should be small.
Applicant
Due to its superior acid resistance and corrosion resistance, high-silicon cast iron has been widely used in chemical anti-corrosion. The most typical grade is STSil5, which is mainly used to manufacture acid-resistant centrifugal pumps, pipes, towers, heat exchangers, containers, valves and cocks.
In general, high-silicon cast iron is brittle, so you must pay great attention to it during installation, maintenance, and use. Hammer must not be used during installation; the assembly must be accurate to avoid local stress concentration; drastic changes in temperature or local heating are strictly prohibited during operation, especially when the temperature rise and fall must be slow when starting, stopping or cleaning; it is not suitable for use as pressure equipment.
High silicon cast iron can be made into various corrosion-resistant centrifugal pumps, Nessler vacuum pumps, plugs, valves, special-shaped pipes and pipe joints, pipes, venturi arms, cyclones, denitrification towers and bleaching towers, concentration furnaces and pre-washing machines, etc. . In the production of concentrated nitric acid, when used as a stripping tower, the temperature of nitric acid is as high as 115-170°C. The concentration of nitric acid processed by the concentrated nitric acid centrifugal pump is as high as 98%. It is used as a heat exchanger and packed tower for mixed acid of sulfuric acid and nitric acid. Part of the heating furnace for gasoline in oil refining production, acetic anhydride distillation tower, benzene distillation tower in triacetate fiber production, acid pump in glacial acetic acid production and liquid sulfuric acid production, as well as various acid or salt solution pumps and cocks, etc.