how to control the performance of castings
The performance of casting alloys including ductile iron is determined by the microstructure containing certain components. To obtain the required performance, you can control the microstructure and make the structure contain a certain amount of alloy strengthening element.
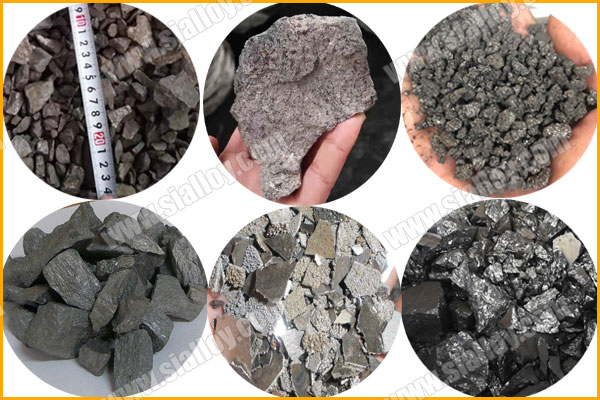
Usually there is always a contradiction between strength and plasticity,with the deepening of the understanding of the alloy strengthened matrix structure, the special requirements for the performance of metal materials continue to increase. The strength of ductile iron is required to reach 600MP or more, and it is required to have good strength and toughness extension. It is difficult to ensure the strength and toughness requirements at the same time through heat treatment,by controlling the factors that affect the microstructure (chemical composition, alloying, melting quality, spheroidizing inoculation, wall thickness conditions, cooling rate, etc.), it can meet as-cast high strength, high toughness requirements.
1.Choice of Chemical Composition
(1) Carbon:The carbon promotes the absorption of magnesium, improves spheroidization,and improves the roundness of graphite balls; improves the fluidity of molten iron, reduces loose defects and shrinkage tendency of castings; can promote graphitization and reduce the tendency of white mouth. However, too high carbon will easily cause graphite to float, which will reduce the overall performance of the casting. Therefore, the carbon is controlled at 3.5%~3.7%.
(2) Silicon: It can promotes graphitization,in the production of ductile iron, the ratio of pearlite to ferrite is changed due to the inoculation of silicon: controlling Si at 2.0%~2.5% is beneficial to the formation of pearlite, and in order to ensure the strength On the basis of 600MP, the elongation rate reaches 10%, and the inoculation effect must be appropriately improved to ensure a certain proportion of ferrite structure and control the silicon at 2.5% to 2.8%.
(3) Manganese:It can stabilize the pearlite element, which can increase the strength and hardness, and reduce the plasticity and toughness. However, manganese is prone to segregation and too much manganese can easily form compounds at the boundary of the eutectic group, which reduces the mechanical properties of the castings. Is serious. Generally, manganese is not used as an element to form pearlite in the as-cast state, and manganese is controlled to <0.5%.
(4) Sulfur:It has a strong affinity with magnesium and rare earths. It consumes spheroidizing elements in molten iron to form MgS and RES slag, which reduces the spheroidization rate; the higher the sulfur, the more spheroidizing agent is consumed, so the high sulfur content in molten iron is caused by the main reason for the poor spheroidization due to the small residual amount of spheroidizing elements; in addition, the high sulfur content is also prone to defects such as slag inclusion and subcutaneous pores,therefore, S<0.03%.
(5) Phosphorus:It has very low solubility in ductile iron, when phosphorus exceeds a certain content, it is easy to segregate at the boundary of the eutectic group to form phosphorus eutectic, which reduces the plasticity, toughness and strength of the casting, and causes cold cracking of the casting,therefore P <0.05%.
(6) Magnesium and RE:There is a certain amount of residual magnesium and RE elements in the molten iron to ensure graphite pellets. In RE magnesium nodular iron, magnesium plays a major role in spheroidization, and RE plays a role in auxiliary spheroidization, and also plays a role in purifying molten iron and resisting interference elements in spheroidization. Control them in the following range: Mg residual 0.030%~0.05%, RE residual 0.030%~0.05%.
2.Melting of Molten Iron
The molten iron is smelted by an intermediate frequency induction electric furnace, and the purest pig iron is used: P, S, interference spheroidizing elements and various alloying elements should be as low as possible; the recycled iron is generally the same material as the riser, scrap or processed iron Swarf, which is convenient for alloy reuse, reduces costs, and is also conducive to the control of molten iron composition; scrap steel should be selected as a single type, clean, free of sand, rust and other debris; alloy copper and tin are the key to whether the product performance can meet the requirements. Without using special nodulizers and inoculants, how to ensure that the alloy is uniform in the molten iron is the basis for product quality and stable performance. Considering that the two alloys will not burn during the smelting process, the alloy should be used in the early stage of smelting. The form is added to the bottom of the furnace for smelting, which can ensure the maximum uniformity of the alloy concentration in the whole molten iron; in principle, the chemical composition of the original molten iron is controlled with moderate CE, high C, low Si, low Mn, P, S, and low interfering element Ti. Bottom, the charge ratio is C: 3.6~3.8%, Si: 1.1~1.5%.
3.Spheroidization and Inoculation Treatment
(1)The selection of spheroidizing agent.The spheroidizing agent is related to the quality of molten iron.the sulfur content in the original molten iron is different, and the spheroidizing agent with different RE content is selected, even if the electric furnace is used for smelting, if the pig iron used contains sulfur and other impurities There are many elements. If the original molten iron contains S>0.03%, FeSiMg8RE7 spheroidizing agent should be used; when S<0.03%, FeSiMg8RE5 or FeSiMg8RE3 spheroidizing agent with low rare earth should be used. The quality of the spheroidizing agent is not only related to the chemical composition, but also has a certain. relationship with the particle size. In the production practice, the particle size is too large and it is not easy to dissolve quickly, which causes the reaction to melt for a long time, causing the spheroidizing agent to float to the surface of the molten iron and burn out. The absorption rate of the spheroidizing agent decreases, which affects the spheroidizing effect; at the same time, the particle size of the spheroidizing agent is too small, especially the proportion of powder form, which must be strictly controlled, because the hot metal temperature is high and it is easy to burn directly, and if the temperature is low, it will be directly oxidized. The particle size of the spheroidizing agent in the production process mainly depends on the size of the spheroidizing bag and the spheroidizing temperature: 300Kg spheroidizing bag is used in the production process, and the spheroidizing temperature is 15100C~15400C, so the particle size of the spheroidizing agent is 5~30 mm or 5-35mm. The spheroidizing agent with over-standard particle size should be less than 5%.
(2)Inoculation treatment. The commonly used inoculation agent is 75FeSi, in order to improve the inoculation effect and reasonably control the final silicon amount. According to the production conditions, the secondary inoculation treatment method is adopted: 0.4% of the inoculation agent is added to the surface of the spheroidizing agent when spheroidizing is adopted. The particle size of the inoculant is 3~8 mm. When it is flushed into the molten iron for spheroidization, the inoculation will occur at the same time. When the molten iron is transferred from the spheroidizing ladle to the pouring ladle before pouring, 0.2~0.3% of the particle size is 1 The ~3mm inoculant is used as the second inoculation, which can effectively prevent the inoculation decline and improve the inoculation effect. Since the performance of as-cast high-strength and high-toughness ductile iron castings is mainly ensured by the microscopic matrix structure after alloying, the amount of pearlite and the strength of the ferrite matrix mainly depend on the role of alloyed copper and tin. It is beneficial to strengthen the inoculation effect appropriately. Under the premise of ensuring the tensile strength of 600MP, the casting has strong toughness, elongation> 10%, and can effectively eliminate carbides, which is conducive to the supply of molten iron, reduces the tendency of molten iron to shrink, and prevents the casting from being loose.
Anyang Huatuo Metallurgy has in the raw materials for gray and ductile castings for more than 10 years, can supply the SiMn,FeP, FeS2, Recarburizer, sphoridizing agent, inoculants etc, if you have any requirement, welcome for your consult.