silicon carbide manufacturing process
Silicon Carbide has stable chemical properties, high thermal conductivity, low thermal expansion coefficient and good wear resistance. Its Mohs hardness is 9.5, second only to diamond. Pure silicon carbide is a colorless and transparent crystal. The crystal structure is divided into exile or rhombohedron. There is very little natural silicon carbide, and most of the materials used in industry are synthetic materials. Commonly known as carborundum. At present, the silicon carbide produced in China's industry is divided into black silicon carbide and green silicon carbide.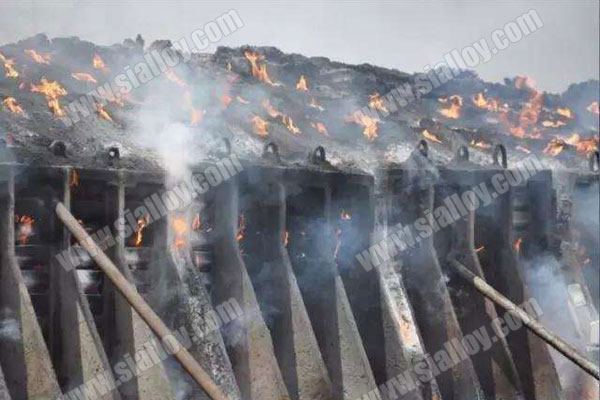
There are three main types of raw materials used in the manufacture of silicon carbide: main raw materials, including silica and graphitized petroleum coke carbon; auxiliary materials, including wood chips and salt; recycled materials, including various silicon carbide scraps. The main raw materials are indispensable and they provide basic Participants in chemical reactions. Auxiliary materials do not directly participate in the basic chemical reaction process. Sawdust only keeps the charge air permeable, and salt only promotes the formation of green silicon carbide. They can be used less or not under certain conditions. The rational use of recycled materials can save some raw materials and help reduce production costs.
Silica sand is one of the main raw materials for the production of silicon carbide, which is processed from natural silicon-containing materials. Its main component is silicon dioxide SiO2. Its most common and most widely distributed form on the earth is quartz stone. Quartz stone accounts for 12% of the earth's crust. From the analysis of chemical composition, nearly 60% of the earth's crust is silica. However, the purity of the silica sand used in the manufacture of silicon carbide needs to be above 98.5%. The second raw material is carbon, the main forms are petroleum coke, metallurgical coke, pitch coke, graphite, charcoal, etc. The carbon materials required for the production of silicon carbide require high carbon content, low ash content and high specificity. Because the higher the density, the smaller the corresponding volume, so you can make more space in the smelting furnace to fill more other materials. The power of the furnace body of a large-scale silicon carbide smelting furnace is generally 10,000kw, and the power consumption for each kilogram of silicon carbide produced is 6-7 kWh. The production cycle is 32 hours for heating and 24 hours for cooling. The above raw materials pass through SiO2+C=SiC+CO in the resistance furnace, and the reaction temperature should be maintained at about 2000 to 2500 degrees Celsius.