the reduction reaction of silicon in blast furnace steelmaking
The process of blast furnace steelmaking is the process of deoxidizing and reducing iron oxides to metallic iron. Metallic iron is extracted from iron ore. The metallic iron in iron ore exists in the state of iron oxide. Therefore, extracting metallic iron from iron oxide is the most basic reaction for smelting pig iron. At present, ferro silicon, silicon briquette or other reducing agents are mainly used to deprive iron ore of oxygen, which is the basic method of blast furnace steelmaking.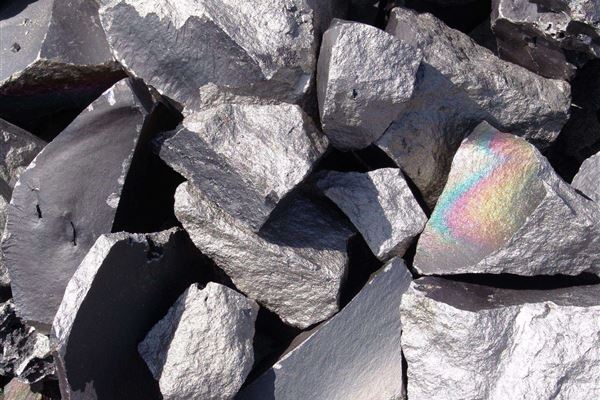
However, elements such as silicon, manganese, and carbon added in steelmaking also need to be reduced. The silicon element enters the molten iron through the addition of ferro silicon, silicon briquette, silicon manganese and other products. Different steel grades have different requirements for silicon content. Generally, the silicon content of steel-making pig iron should be less than 1%. At present, blast furnace smelting low-silicon pig iron can control the silicon content to about 0.2%, or even below 0.1%. Casting pig iron requires silicon content between 1.25%-4%, and the requirement for ferro silicon is that the higher the silicon content, the better. The silicon in pig iron mainly comes from the gangue of the ore and the SiO2 contained in the coke. Under special circumstances, silica can also be added to the blast furnace. SiO2 is a relatively stable compound, its decomposition pressure is very low, and the heat of generation is very large. Therefore, Si is more difficult to reduce than Fe, Mn and other elements. SiO2 can only be directly reduced by fixed carbon at high temperature. The SiO formed by reduction can volatilize into gas, and the temperature near the tuyere of the blast furnace is higher than 1900°C, so the volatilization condition of SiO is sufficient. In addition, gaseous SiO can also improve the contact conditions with coke, which is beneficial to the reduction of Si.
The reduction of SiO2 can also be carried out by means of the reduced Si, and the reaction process is SiO2+Si=2SiO. The unreduced SiO is re-oxidized in the upper part of the blast furnace and condenses into white SiO2 particles. These particles can be collected to make Silica Fume for concrete and other industries. When ferro silicon is smelted, the volatilization amount of SiO2 is also very high, which can reach 25%. Due to the presence of Fe in the blast furnace, the reduced Si and Fe form a very stable silicide FeSi at high temperatures and dissolve in the iron, which can reduce heat consumption and temperature, thereby contributing to the reduction of Silicon.