inoculation of cast iron
Inoculation is a method used to control the structure and properties of cast iron. Cast iron inoculants produce their inoculation effect by significantly increasing the number of nucleation points suitable for graphite growth during eutectic solidification.These effects will become very obvious due to the significant increase in the number of eutectic grains in gray iron and the number of graphite spheres in ductile iron,this will lead to a reduction in the degree of subcooling, thereby minimizing the risk of iron carbide or white mouth formation in the casting, especially in the case of fast cooling thin-walled castings. The most effective inoculant is FeSi alloy containing a small amount of one or several elements (such as Ca, Ba, Sr, Zr and/or Ce).
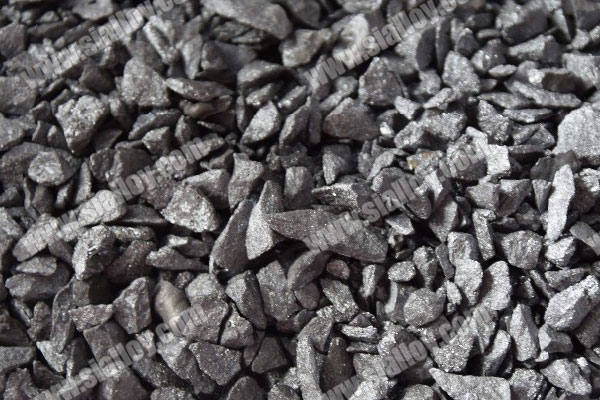
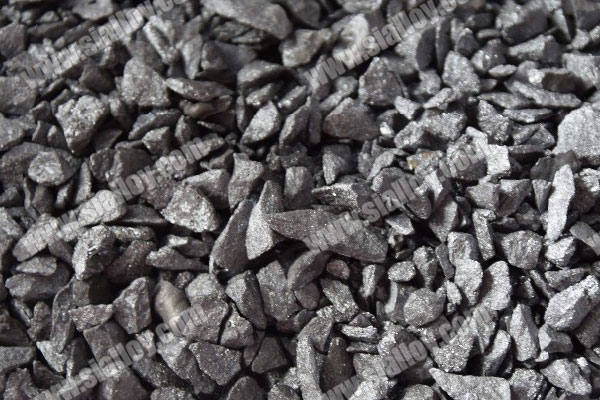
The inoculation of cast iron is generally divided into two inoculations, namely, the first inoculation in front of the furnace (also called ladle inoculation) and the second inoculation (also called the late inoculation or the instantaneous inoculation ). Due to the long time interval between the inoculant addition and the pouring, it is prone Inoculation decline, in order to overcome the decline of inoculation effect caused by inoculation decline over time, so the second inoculation is usually adopted, and the flow inoculation is a common secondary inoculation method.
Ladle Inoculation
Since the length of time involved in the delivery of molten iron ladle cannot be eliminated, it is necessary to add a relatively large amount of inoculant in order to make up for the loss of decline. The addition amount ranges from 0.2% of most gray iron to 0.75% of the most demanding ductile iron. The inoculation alloy should be selected according to the size of the molten iron ladle, and should be dust-free to avoid losses due to oxidation and hot airflow. Under normal circumstances, ladle of less than 300 kg can be 1-3mm in size, and ladle of more than 300 kg is recommended to be 3-8mm in size.
Note: The inoculant should never be added to the bottom of the ladle before tapping, especially when the ladle is still red and hot or there is still a small amount of molten iron left from the previous casting in the ladle.
When inoculating ductile iron, it is very important that the inoculant must be added after the Mg reaction is completed. Adding together with the spheroidizing agent or adding it when the reaction is taking place will greatly reduce the effectiveness of the inoculant and may result in an increase in the carbide content of the casting. In the case that the spheroidizing agent and the inoculant must be added to the same ladle, when about 2/3 of the molten iron has been poured on the spheroidizing agent, the iron should be stopped. Then wait until the reaction is over, and then add the inoculant to the remaining molten iron stream.
Flow Inoculation
Flow inoculation is to add the powdery inoculant to the top of the sprue cup along with the flow of iron. Under normal circumstances, the amount of gray iron is 0.02-0.05%, and the amount of ductile iron is 0.05-0.2%. In general, the particle size of the inoculant must be specifically set at 0.2-0.7mm to ensure its rapid dissolution in molten iron and good fluidity through the application of machinery.
Anyang Huatuo Metallurgy has been engaged in the production and sales of foundry materials for more than ten years,can provide high quality ferro silicon and silicon barium inoculant. It has always been adhering to the tenet of quality first and serving customers with integrity. If you have any related questions, please feel free to consult.