desulfurization and deoxygenation of steelmaking
The basic tasks of steelmaking are decarburization, dephosphorization, desulfurization, and deoxygenation, removing harmful gases and non-metallic inclusions, raising the temperature, and adjusting the composition of the molten steel. Oxygen supply, slagging, stirring, and alloying are the means to complete the task of steelmaking.
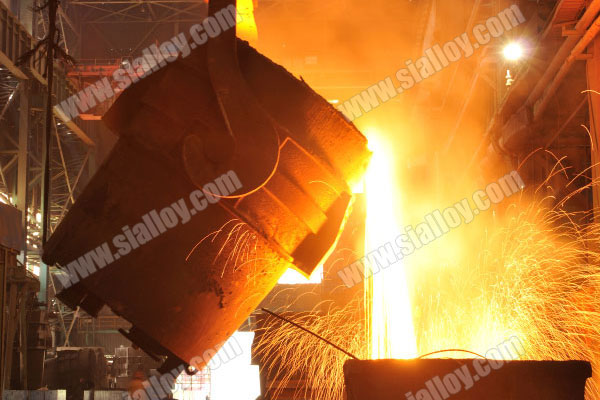
What is the significance of the decarburization reaction to the steelmaking process?
The carbon in the molten iron is oxidized by decarburization reaction to be close to or equal to the specification range of carbon in molten steel when tapping.
Circulating agitation of the molten pool.
The generated CO is necessary to remove the gas in the steel.
Conducive to the elimination of non-metallic inclusions in steel.
Provide heat source for steel-making reaction.
It is conducive to the reaction between slag and steel during the blowing process.
What effect does oxygen have on the performance of steel?
The solubility of oxygen in solid iron is very small, mainly in the form of oxide inclusions. Therefore, most of the inclusions in steel are oxides except for some sulfides. Non-metallic inclusions are the main source of damage to steel, and have significant adverse effects on the fatigue strength, processing performance, ductility, toughness, welding performance, HIC resistance, and corrosion resistance of steel. If the oxygen content is high, the continuous casting billet will also produce defects such as subcutaneous bubbles, which deteriorates the surface quality of the continuous casting billet.
Why should molten steel be deoxidized?
Without the deoxidation of molten steel, the continuous solidification structure will not be obtained. High oxygen content in steel will also produce defects such as subcutaneous bubbles and looseness, and exacerbate the harmful effects of sulfur. The generated oxide inclusions remain in the steel, which will reduce the steel's plasticity, impact toughness and other mechanical properties. Therefore, it is necessary to remove excess oxygen in the steel.
What are non-metallic inclusions? Where does it come from?
The non-metallic phase generated or mixed in the smelting, casting and molten steel solidification process is called non-metallic inclusions. The non-metal phase is a compound of some metal elements and Si, combined with non-metal elements, such as oxides, nitrides, sulfides, etc. Due to the presence of inclusions, the continuity of the steel matrix is destroyed, resulting in the unevenness of the steel structure, which affects the mechanical properties and processing properties of the steel. However, non-metallic inclusions also have a beneficial effect on steel, such as controlling intrinsically fine grains, precipitation hardening, promoting grain orientation, and improving the cutting performance of steel.
What are the ways to reduce oxide inclusions in steel?
To reduce oxide inclusions in steel, foreign inclusions should be minimized. Improve the purity of raw materials; adopt reasonable smelting process, deoxidation system and molten steel refining process according to the requirements of steel types; improve the quality and performance of refractory materials used in converters and casting systems; reduce and prevent secondary oxidation of molten steel and maintain normal Pouring temperature, implementing full-process protective pouring, choosing protective slag with good performance; selecting reasonable steel thermal processing and heat treatment processes are conducive to improving the properties of inclusions and improving steel quality.
Why is slag making for steel making?
The first step in making steel is to make good slag. The completion of all steelmaking tasks is almost related to slag. The purpose of steelmaking and slagging:
remove harmful elements P and S in steel
steelmaking slag covers the surface of the molten steel, protects the molten steel from excessive oxidation, does not absorb harmful gases, keeps heat, and reduces the burning of beneficial elements.
Absorb the floating inclusions and reaction products.
Ensure that the carbon-oxygen reaction proceeds smoothly.
It can reduce the corrosion loss of furnace lining.
There are also others need to notice, such as the content of sulfur and phosphorus, sometimes the deoxidizer can also be used to remove sulfur and phosphorus.