the desulfuration inside blast furnace
Sulfur is a harmful element in pig iron. High-sulfur pig iron produces hot brittleness during casting and also reduces the filling performance of molten iron during casting. For steel-making pig iron, it is difficult to desulfurize the steel-making process. Ensuring to obtain qualified molten iron with sulfur is an important task in blast furnace smelting. The sulfur in the blast furnace comes from ore, coke and injection fuel, and the flux will also bring a small amount of sulfur into the smelting process using natural minerals. The total amount of sulfur brought in by the charge when smelting pig iron is called the sulfur load.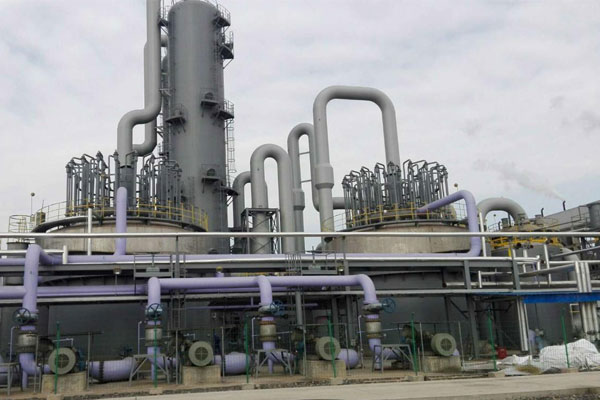
The amount of sulfur carried by coke in the charge is the most, accounting for 60%-80%, while the sulfur carried by ore generally does not exceed one-third. If the injection fuel is heavy oil, the sulfur content is very small, if it is Pulverized Coal Injection brings more sulfur. The overall sulfur load should be controlled below 10kg per ton of iron. The sulfur in coke is mainly organic sulfur, and the other part exists in the ash in the form of FeS and sulfate. The sulfur in the ore and flux mainly exists in the form of Iron Pyrite (FeS2), and a small amount is in the form of sulfide of calcium sulfate, barium sulfate and other metals such as Cu, Zn, and Pb. With the decrease of the charge, part of the sulfur gradually volatilizes into the gas. When the charge reaches the tuyere, the remaining sulfur is generally 50%-70% of the original sulfur content. This part of sulfur is burned in front of the tuyere to generate SO2 and enter the gas. Then the bottom of the furnace is reduced by fixed carbon to generate CO gas and sulfur vapor, and then a part of it comes into contact with other substances and decomposes. Finally, the remaining sulfur exists in the molten iron in the form of FeS.
The level of sulfur in molten iron depends on many aspects. Sulfur load has a direct relationship with the quality of pig iron. The less sulfur contained in ore, fuel and charge, the lower the sulfur content of pig iron and the better the quality of pig iron. At the same time, due to the reduction of the sulfur load, the desulfurization burden of the slag can be reduced, thereby reducing the amount of flux and reducing the output of the slag, which is beneficial to reducing fuel consumption and prolonging the service life of the furnace body.