factors affect dissolution and diffusion of recarburizers
In the process of smelting synthetic cast iron, due to the large amount of scrap added and the low content of C in the molten iron, the recarburizer must be used to increase carbon.The carbon in the recarburizer is in the form of a simple substance, and the melting temperature is 3727℃, which cannot be melted at the temperature of the molten iron,therefore, the carbon in the recarburizer is mainly dissolved in the molten iron through dissolution and diffusion.When the graphite recarburizer content of molten iron is 2.1%, graphite can be directly dissolved in molten iron. The direct dissolution of non-graphite carbonization basically does not exist, but as time passes, carbon gradually diffuses and dissolves in molten iron.For the recarburization of cast iron smelting in an induction furnace, the recarburization rate of using crystalline graphite is significantly higher than that of non-graphite recarburizer.
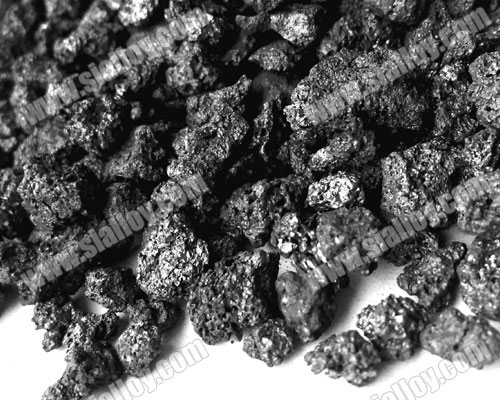
There are many factors that affect the effect of recarburizer.
(1)Particle size of recarburizer.The absorption rate of the recarburizer depends on the combined effect of the dissolution and diffusion rate of the recarburizer and the rate of oxidation loss. In general, particle size of recarburizer is small, the dissolution rate is fast, and the loss rate is large;particle size of recarburizer is large, the dissolution rate is slow, and the loss rate is small. Generally speaking, if the diameter and capacity of the furnace are large, the particle size of the recarburizer should be larger,on the contrary, the particle size of the recarburizer should be smaller.
(2)The influence of the amount of recarburizer added. Under a certain temperature and the same chemical composition, the saturation concentration of carbon in the molten iron is constant. Under a certain degree of saturation, the more recarburizer is added, the longer the time required for dissolution and diffusion, the greater the corresponding loss, and the lower the absorption rate.
(3)The influence of temperature on the absorption rate of recarburizer. In principle, the higher the temperature of the molten iron, the more conducive to the absorption and dissolution of the recarburizer. On the contrary, the recarburizer is difficult to dissolve and the absorption rate of the recarburizer decreases. However, when the temperature of the molten iron is too high, although the recarburizer is easier to fully dissolve, the rate of carbon burnout will increase,which will eventually lead to a decrease in the carbon content and the overall absorption rate of the recarburizer. Generally, when the molten iron temperature is 1460 to 1550℃, the recarburizer absorption efficiency is the best.
(4)The influence of stirring of molten iron on absorption rate of recarburizer. Stirring facilitates the dissolution and diffusion of carbon, and prevents the recarburizer from floating on the surface of the molten iron and being burned. However, if the stirring time is too long, it will not only have a great impact on the service life of the furnace, but after the recarburizer is dissolved, the stirring, will aggravate the loss of carbon in the molten iron. Therefore, the proper stirring time of molten iron should be to ensure that the recarburizer is completely dissolved.
(5)The influence of the chemical composition of molten iron on the absorption rate of recarburizer. When the initial carbon content in the molten iron is high, the absorption speed of the recarburizer is slow, the absorption amount is small, the burn loss is relatively large, and the absorption rate of the recarburizer is low under a certain solubility limit; when the initial carbon content of the molten iron is low, the situation is reversed. In addition, the silicon and sulfur in the molten iron hinder the absorption of carbon and reduce the absorption rate of the recarburizer; while the manganese element helps the absorption of carbon and improves the absorption rate of the recarburizer. In terms of the degree of influence, silicon is the largest, followed by manganese, and carbon and sulfur have less influence. Therefore, in the actual production process, manganese should be added first, then carbon, and then silicon.
The high-quality graphite recarburizer can not only improve the mechanical properties of the castings, improve the metallographic structure, but also improve the processing properties of the castings. Therefore, it is recommended to use high-quality graphite recarburizers when producing cylinder blocks, cylinder heads and other key products in the induction furnace smelting process.
Anyang Huatuo Metallurgy has new type graphite recarburizer in columnar, the carbon content 90% or 95% with low content of sulfur 0.08% or 0.05%, if any interests, welcome for consult.