casting inoculant
Nowadays, there are many types of casting inoculants for the treatment of gray cast iron, but 75 ferrosilicon is the most widely used. In recent years, the demand for thin-walled castings is increasing, and the requirements for inoculation treatment are also more stringent. In the case of low carbon equivalent of cast iron, inoculant contains cerium, lanthanum, cerium, zirconium or a certain rare earth element is used. Can better control the tendency of the white fracture at the thin wall. It has also been reported that the use of casting inoculants containing strontium, barium and rare earth elements can slow down the decline of gestation. In addition, the dosage of carbon inoculants has also increased.At present, the mainstream gray cast iron inoculants on the market are mainly the following:
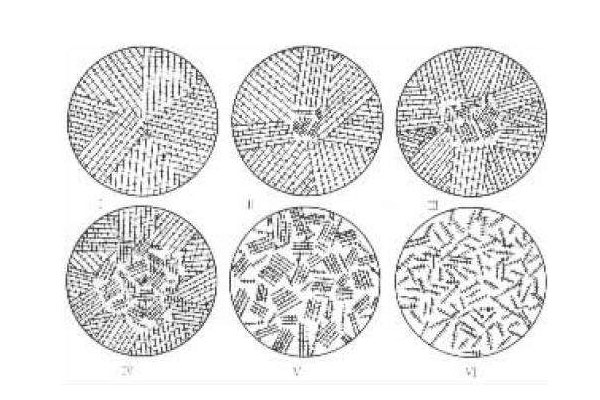
75 ferrosilicon is the most commonly used casting inoculant. The aluminum and calcium content play an important role in the inoculation effect. It is reported that the ferrosilicon without aluminum and calcium has little or no effect on the gray cast iron. It is generally believed that in molten iron, aluminum and calcium react with oxygen and nitrogen to form a compound with a high melting point, which becomes the core of graphite crystal.
Ferrosilicon 75, as an casting inoculant, the US standard stipulates that the aluminum content is 0.75-1.75%, and the calcium content is 0.5-1.5%. There are different models of China's ferrosilicon standards. The upper limit of aluminum content are 0.5%, 1.0%, 1.5% and 2.0%. The upper limit of the calcium content is 1.0%. However, the aluminum content in the molten iron should not be too high, and the addition of 0.01% aluminum may cause subcutaneous pores in the casting.
The bismuth-containing ferrosilicon has a strong ability to eliminate white mouth, and its usage is half that of ferrosilicon.
The bismuth-containing ferrosilicon also has a strong ability to promote graphitization, and the strontium content is generally 4 to 6%. The amount used is slightly smaller than that of ferrosilicon.
Ferrosilicon containing zirconium: Zirconium has deoxidation effect, which is beneficial to improve the fluidity of molten iron, can reduce the white mouth tendency of cast iron, and promote uniform and fine A-type graphite. And there is also the role of slowing down the decline. There are also zirconium-containing ferrosilicon in China, but there are still few adopters.
Silicon Germanium Alloy
The use of 20-30% silicon germanium alloy as an casting inoculant which can significantly reduce the white fracture tendency of cast iron, and can increase the time of maintaining the inoculation effect to about 30 minutes, which is especially suitable for large castings. The alloy was added in an amount of about 0.1% in process.
Silicon Calcium Alloy
Although the silicon-calcium alloy has a strong inoculation effect, in addition to the support core wire application, it is not suitable to use the granular alloy as the inoculant for the cast iron. The main disadvantages are:
- The density is much lower than that of molten iron, and it is easy to float to affect the effect of the remaining molten iron;
- The tendency to form slag is large;
- The gestational effect declines rapidly;
- The amount of addition required for the treatment is large, about 0.3-0.5%. An very common casting inoculant.
Rare Earth Inoculant
The rare earth metal-containing inoculant such as rare earth mixed metal and rare earth ferrosilicon has a strong inoculation effect when added in an appropriate amount, and the effect can be several times of 75 ferrosilicon, which can effectively eliminate white mouth and slow down the decline of the inoculation effect. If the amount is too high, the cast iron may be too cold during crystallization, and cementite structure may appear. The dosage must be strictly controlled during use.
Carbon Inoculant
The carbon inoculant is mainly used for pretreatment before cast iron inolucation, and is generally a crystalline carbonaceous material. According to research reports, for gray cast iron, 85-90% of metallurgical silicon carbide has the best effect, and crystalline graphite is also effective. The amount of addition during pretreatment is generally from 0.75 to 1.0%.