alloy cast iron
Cast iron refers to a multi-element iron-based alloy with carbon content greater than 2.11% and more elements such as silicon, manganese, etc.; cast iron has a simple production process and low cost, and is the earliest used and most widely used steel material. Compared with carbon steel, cast iron contains more impurity elements such as sulfur and phosphorus. With the development of industry, the requirements for the properties of cast iron are getting higher and higher, that is, not only is it required to have higher mechanical properties, but sometimes it is also required to have some special properties, such as high wear resistance, heat resistance and corrosion resistance, etc. . In order to further improve the mechanical properties or special properties of cast iron, alloy elements can also be added, or the content of elements such as silicon, manganese, and phosphorus can be increased. This kind of cast iron is called alloy cast iron. Compared with alloy steel used under similar conditions, alloy cast iron is easy to melt, low in cost, and has good performance. But most of them have greater brittleness and poor mechanical properties.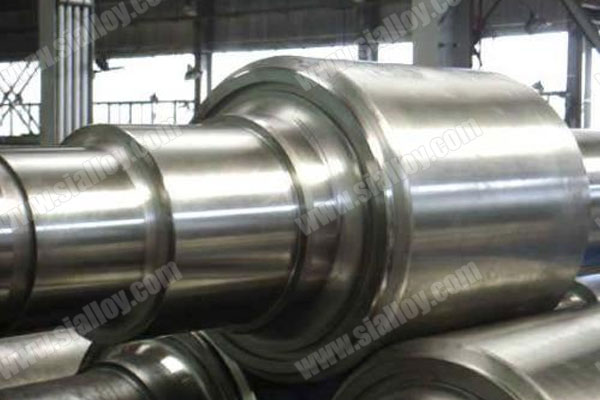
Alloy cast iron refers to cast iron with special properties by adding alloy elements to ordinary cast iron. Commonly added alloying elements are silicon, manganese, phosphorus, nickel, chromium, molybdenum, copper, aluminum, boron, vanadium, titanium, antimony, tin and so on. Alloy cast iron is divided into low alloy cast iron (alloying element content <3%) and medium alloy cast iron (alloying element content> 10%) according to the added amount of alloying elements. Alloying elements can change the matrix structure of cast iron, so that cast iron has special physical-chemical properties such as heat resistance, wear resistance, corrosion resistance, non-magnetic and low temperature resistance, so this cast iron is also called "special performance cast iron". The addition of elements that can form a dense oxide film in cast iron, such as Si, Cr, Al, etc., can improve the oxidation resistance of cast iron. Low-chromium (Cr: 0.5-1.9%) or low-chromium and low-copper alloy cast iron is commonly used for heat-resistant castings that work at 500-700℃. For parts that work at >800℃, alloy cast iron with high silicon (Si>5%), high aluminum (Al: 25%) and high chromium (Cr: 32-36%) are mainly used. At present, alloy cast irons such as silicon and silicon-aluminum are widely used, and they have good heat resistance and high-temperature strength. Some cast iron factory used to use ferro silicon as additive of Si element, but recent years, many factory start to use silicon carbide in order to save production cost, and the real effect is quite impressive.
The range of application of alloy cast iron is very wide. Because of their superiority and economy in use, they have replaced steel castings, forgings and malleable iron castings in some cases. Alloy cast iron is widely used in machinery manufacturing, metallurgical mines, chemical industry, instrument industry and refrigeration technology sectors. In most cases, alloy cast iron has replaced non-alloy cast iron. Such as: power machines, chemical equipment, pumps and compressors. Rolling research equipment and wear-resistant castings, machine tools, metal processing molds, etc.