RE magnesium silicon alloy
According to the production method, the spheroidizing agent can be divided into several different types as followings:
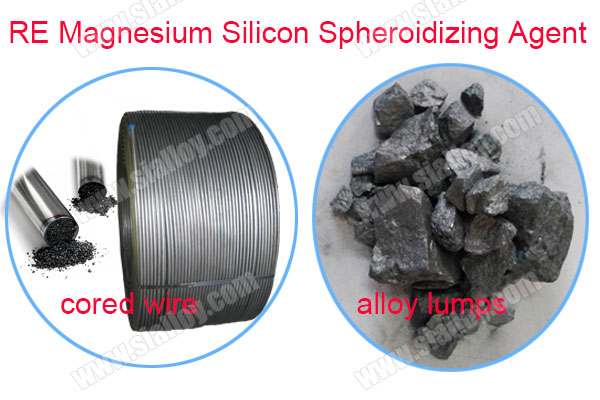
1.RE Magnesium Silicon Alloys
It is currently the most widely used spheroidizing agent in the world.Initial the RE/Mg ratio in Chinese production has a large range (0.5~2.2), the RE/Mg ratio of foreign production has a small range (0.1~0.3), At present, after standard revision, all RE silicon magnesium spheroidizing agents produced in China meet RE/Mg not more than 1.
2.The calcium-magnesium spheroidizing agent is mainly produced and applied in Japan. For example, the calcium-based alloys NC5, NCl0, NCl5, NC20, and NC25 produced by Shin-Etsu (SHIN-ETSU) have magnesium content ranging from 4 to 28%, but the calcium content changes slightly. , The variation range is 20~31%; this kind of alloy has a small tendency to white mouth, but requires high processing temperature and large amount of slag after processing.
3.Nickel-magnesium alloys are used in the Americas and Europe. The nickel-magnesium alloys produced by the United States International Nickel Company are up to 82-85%, of which Mg and Ca are 13-16, and 20 respectively, and the lowest nickel-magnesium alloy is 57-61% (Mg4 .0~4.5%, Ca<2.5, Fe32~36). In the nickel-magnesium alloy produced by German Metal Chemical Company, Ni is 47~51%, Mgl5~17%, C1.0% Si28~32%, RE1.0% Fe. The advantages of these alloys are their high specific gravity and stable response. Nickel can be used for alloying. Their characteristic is that they are expensive. This alloy is basically not used in China.
4.Pure magnesium alloys must be treated with a special pressure and a magnesium bag. The absorption rate of magnesium is high, but the handling safety measures must be extremely strict, and the proportion of applications in production is small. Rare earth is the spheroidizing agent used when inventing ductile iron, and its discovery promoted the process of industrial application of ductile iron. However, the price is high and the white mouth tends to be high. Excessive excess will make graphite metamorphose. Now it is not used as a spheroidizing agent alone, but only as an auxiliary spheroidizing element.
5.Briquetting spheroidizing agent
Direct pressure molding with magnesium powder and iron powder and the designed silicon content. This spheroidizing agent contains very low silicon, and is usually called a low-silicon briquette spheroidizing agent, which provides a large room for subsequent incubation , It is beneficial to the production of as-cast ductile iron, but this alloy is easy to float and the treatment effect fluctuates greatly. It is best to mix it with a block spheroidizing agent during treatment.
6.Spheroidizing agent cored wire
The magnesium powder and iron powder are coated in thin steel plates or steel plates, and they are quickly fed into the molten iron to achieve the purpose of spheroidization. This spheroidizing agent is more expensive and requires a large investment in equipment, but the alloy has a high absorption rate during processing. The total cost of processing ductile iron has almost no increased.
7.Powdered spheroidizing agent
This spheroidizing agent is a Russian patent. When used, the magnesium powder and the inhibitor are mixed into the bag, and the molten iron flows through the surface of the alloy, and the alloy is reflected layer by layer to achieve the spheroidizing effect. This special process is called For MC.
At present, pyro-metallurgical alloys are mainly used in the production of ductile iron in China and abroad.Briquetting spheroidizing agents, cored wire spheroidizing agents, and powdery spheroidizing agents are rarely used. The spheroidizing agent used in pyrometallurgy accounts for more than 90% for the production, if any need can contact Anyang Huatuo Metallurgy, who owned ISO9001:2015 certificate for more than 20 years.