the influence of pouring temperature on casting
There are many influencing factors in the production of gray cast iron. Here mainly introduces the impact of casting temperatures.
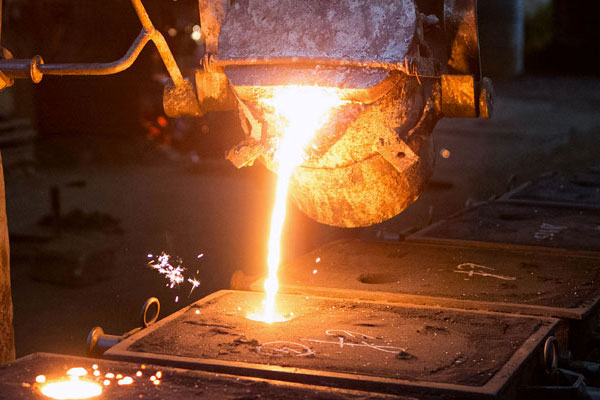
The casting temperature is high, which causes the sand to rise, especially the gray cast iron with complex sand core. When the cast temperature is more than 1420℃, the waste is 50% when the casting temperature is 1460℃. In production, the ferrite temperature can be better controlled by the induction electric furnace smelting.
Defects that may be formed when temperature is too low.
(1)Vulcanized manganese gas. Such a pore is located below the gray cast iron nipple and is mostly above, and it is often revealed after processing, and the air hole is about 2 to 6 mm. Sometimes a small amount of slag, metallographic studies have shown that this defect is mixed by MNS segregation with slag, which is that the casting temperature is low, and the iron fluid contains Mn and S amount high. Such a S-containing and suitable Mn content (0.5% to 0.65%) can significantly improve the purity of the iron solution, thereby effectively preventing such defects.
(2)The air hole caused by a sand core gas. The air pores and multidimensional pores often cause due to poor sand core. Since the core is hardened in the core box during the core, this often makes the number of sand core exhaust holes are not enough. In order to form an exhaust hole, the drilling can be supplemented after the core is hardened.
(3)After the liquid sizk is processed, the gray-cast metal is found to be a small hole of the monomer, and the diameter of the hole is generally 1 to 3 mm. There is only 1 to 2 small holes in individual cases. The phase studies have shown that these small holes appear together with a small amount of liquid clamping, but the segregation of S is found. Studies have shown that this defect is related to the casting temperature, and the casting temperature is not found in the casting temperature, so the casting temperature should be controlled at 1380-1420 ° C. It is worth mentioning that changing the design of the casting system, failing to eliminate this defect, so the defect can be considered to form heat due to the low casting temperature and the iron solution is pouring under a trace amount of water.
The most common cause of pouring temperatures is before pouring, the iron solution is transported and resorts over the open boat. The heat loss can be significantly reduced using a waterphed cover with a heat insulating material.
Anyang Huatuo Metallurgy focus on raw materials of casting for more than 20 years, if there are any confused welcome for consulting us.