the effect of boron in cast iron production
Boron alloy cast iron has high wear resistance. The reason is that high-hardness boron carbides in the form of hard particles undergo wear during the wear process and become the first sliding surface, while pearlite has a large hardness difference with carbides. Therefore, poor wear occurs and becomes the second sliding surface. The fine recesses after pearlite wear are often filled with lubricating oil, which can supplement the first sliding surface and reduce the tendency of the oil film on the first sliding surface to be cut off. This not only reduces the wear and tear of the province, but also makes the mating material less likely to wear. In addition, the melting point of boron carbide is much higher than that of phosphorus eutectic, and its corrosion resistance is better. Therefore, boron-containing cast iron is often used in the manufacture of cylinder liners and other products, and its life is more than 50% higher than that of high-phosphorus cast iron.
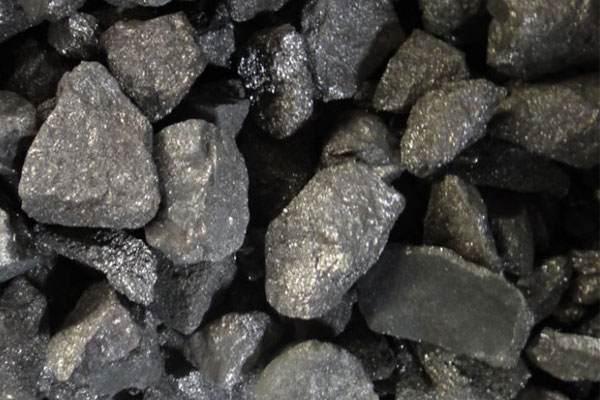
Different content of boron in cast iron has different effects on cast iron:
Boron has a strong inhibitory effect on the graphitization of cast iron. Adding 0.1-0.4% of boron iron can increase the whiteness of cast iron by 3-10mm. Boron hinders the decomposition of cementite during annealing, and when the boron in malleable cast iron is greater than 0.01%, it hinders annealing graphitization. The matrix structure of the cast iron hardly changes after adding boron. When the boron content is 0.136%, the cast iron still has a gray-white fracture, that is, fine pearlite plus a very small amount of ledeburite and a certain amount of unique carbide and graphite.
Some foreign manufacturers add 0.03-0.08% boron to ordinary gray cast iron or high-phosphorus cast iron, and use this material to make cylinder liners, piston rings and other parts. This is because the wear resistance of low-boron cast iron is higher than that of ordinary gray cast iron. 5 times, the composite cementite is formed after adding boron, which further improves the wear resistance of cast iron.
When the boron content of ordinary white cast iron is less than 0.25%, the strength and toughness change little. When the boron content exceeds 0.3%, the strength and toughness drop sharply. The carbides in boron-containing white cast iron exist in the form of a network. The carbides split the continuity of the matrix, increase the brittleness of the cast iron, and reduce the strength and toughness.
Different elements have different effects on cast iron. Therefore, the control of various elements of alloy materials added to cast iron is particularly important. Anyang Huatuo Metallurgy has been engaged in various cast iron raw materials for more than ten years, always upholding responsibility to uphold quality and sincerely serve customers , If you have any needs, please feel free to consult.