smelting control of intermediate frequency electric furnace
A reasonable smelting process should be compiled according to the metallurgical characteristics of the intermediate frequency electric furnace. From charging, temperature control, and adding alloys, recarburizers, slag removers, and tapping temperature at different temperatures, all links are strictly controlled, and strive to use the shortest smelting time , Minimal alloy burning loss and oxidation, to achieve the purpose of controlling and stabilizing the metallographic structure and improving the quality of castings.
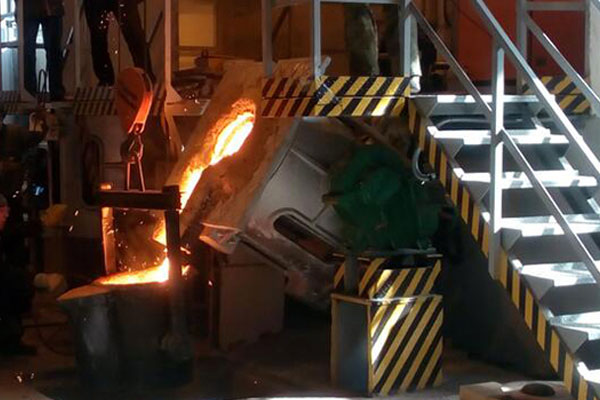
In production practice, we divide the entire smelting process into three phases for temperature control. The so-called three-stage temperature here refers to: melting temperature, slagging temperature and tapping temperature.
1.Melting temperature: The melting period before the sampling temperature determines the balance between the absorption of alloying elements and the chemical composition. Therefore, high-temperature melting and feeding should be avoided to avoid scaffolding. Otherwise, the molten iron will be in a boiling or high temperature state, the carbon element will burn more, silicon will continue to be reduced, the oxidation of the molten iron will increase and the impurities will increase. According to the process requirements, the melting temperature is controlled below 1360 degrees Celsius, and the sampling temperature is controlled at about 1420 degrees Celsius. If the sampling temperature is low, the iron alloy is not melted, and the chemical composition of the sample is not representative; if the temperature is too high, the alloy will burn or reduce, which will also affect the composition adjustment during the scouring period. After sampling, the power of the intermediate frequency furnace should be controlled. After the quality management instrument in front of the furnace showed the result of the chemical composition, it just entered the slagging temperature.
2.Slagging temperature: The slagging temperature is an important part of determining the quality of molten iron, because it is closely related to the stability of the composition and the effect of the inoculation treatment, and directly affects the control of the tapping temperature. Excessively high slagging temperature aggravates molten iron graphite nucleus burning and silicon reduction, especially for acidic furnace linings. In theory, high silicon content in molten iron will cause carbon emission, which will affect crystallization by temperature, and there will be reflections. If the temperature is too low, the molten iron will be exposed for a long time, and the carbon and silicon will burn seriously. When adjusting the composition again, not only will the smelting time be prolonged to make the molten iron overheat, but also the composition will get out of control, increase the degree of supercooling of the molten iron, and destroy the normal crystallization.
3.Iron tapping temperature: In order to ensure the best temperature for pouring and inoculation, we generally control it at 1520-1550 degrees Celsius. High and low tapping temperature will affect the crystallization and inoculation effect of cast iron. If the temperature is too high, such as exceeding the prescribed temperature by 30℃, although the carbon and silicon are also moderate in the rapid analysis before the furnace, the triangle test piece will be tested. The depth of the white mouth will be too large or the center will show numbness. In this case, even if measures are taken to add carbon to the furnace to increase the inoculum, the effect is not good, and after reducing the intermediate frequency power, the furnace temperature should be reduced, that is, 10% of the total amount of molten iron is added to the furnace- 15% fresh-baked iron, so that the pitting in the heart of the test piece turns to gray, and the depth of the white mouth at the top becomes smaller. If the high temperature lasts for a long time, after the above method is adopted, the carbon replenishment measures in the furnace must still be implemented. The tapping temperature is controlled according to the pouring temperature. The appropriate pouring temperature for shell iron castings is (about 1440 degrees Celsius), which can achieve "high temperature tapping, proper temperature pouring". It is of course the best to strictly control and control. Because the tapping temperature is low, As a result, the pouring temperature is lower than 1380 degrees Celsius, which is not conducive to desulfurization and degassing, and particularly affects the inoculation treatment effect. As the temperature decreases, problems such as cold barriers and unclear contours increase significantly.
Except the temperature control, there are the raw materials need to pay attention for smelting of intermediate frequency electric furnace, such as ferro alloys additive, carbon additive, slag remover, deoxidizer, etc, Anyang Huatuo Metallurgy researched steelmaking raw materials for more than 20 years, if any confused will be glad to exchange experience.