silicon carbide for cast iron
Silicon carbide is also called carborundum, and its chemical formula is SiC. Its molecular mass is 40.1, CAS Number 409-21-2, and its melting point is 2700 degrees Celsius. Its chemical properties are stable, its thermal conductivity is high, its thermal expansion is fast, its abrasion resistance is good. As an abrasive, it can be used as abrasive tools, such as grinding wheels, whetstones, grinding heads, and sand tiles. In the field of metallurgy, it is generally used as metallurgical deoxidizer and high-temperature resistant material. Silicon carbide has the characteristics of corrosion resistance, high-temperature resistance, high strength, good thermal conductivity, and impact resistance. On the one hand, silicon carbide can be used in various smelting furnace linings, high-temperature furnace kiln components, silicon carbide plates, lining plates, strutting piece, saggers, silicon carbide crucibles, etc.
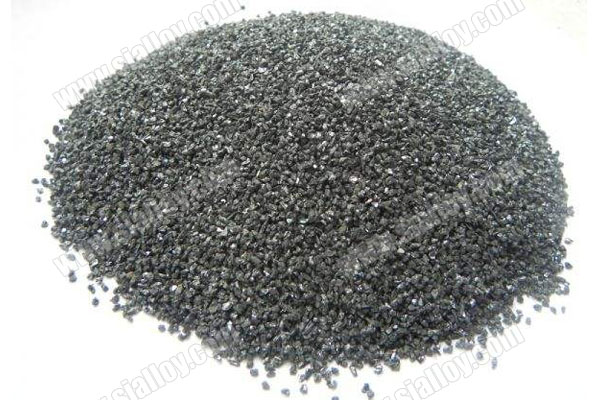
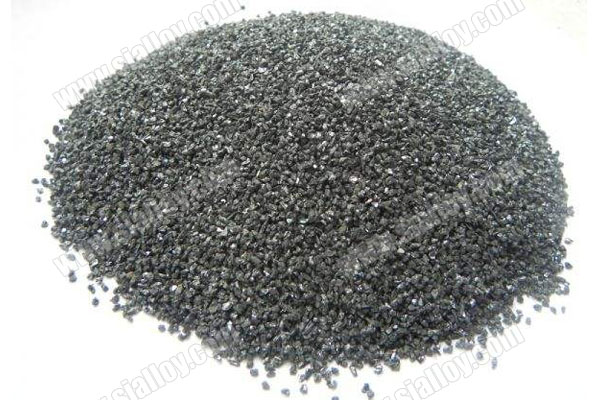
The purity of silicon carbide for cast iron use usually is about 90%. First, high purity materials, high hardness, high melting point, low purity materials may have too many impurities. There is also a kind of recycled silicon carbide, which is cheaper and is made of old electrical devices recovered from silicon carbide. The material used in the electric furnace is best to have finer particles, 0.5-3 mm, so that it is easy to melt and absorb. If used in a cupola, the block size is larger to prevent it from being washed out by strong airflow. At high temperatures, silicon carbide decomposes into carbon and silicon ions. Their chemical properties are to react with oxygen first, so it reduces the oxidation of molten iron, and then enters the molten iron separately, and first becomes the crystal core of graphite. As we all know, both carbon and silicon are They have a strong inoculation effect, so they are very helpful for the melting of electric furnaces and low-carbon silicon hot metal. The added amount of silicon carbide is generally about 0.5-5%. Silicon carbide has been used more in casting production. According to everyone's use, the effect is better, especially in smelting, increasing the graphite core, increasing the number of graphite balls of ductile iron, and improving the graphite form of gray iron. Both are very helpful. Because of the high single silicon carbide, at 2700 degrees Celsius, in the furnace of ordinary casting production, generally not reach such a high temperature. The decomposition of silicon carbide in the casting furnace is a gradual decomposition in a molten state, and the diffusion is relatively slow. Therefore, the time for adding silicon carbide in the furnace is earlier than other alloys. Generally, it is added between one-third and one-half of the furnace smelting, so that silicon carbide for cast iron has sufficient temperature and time decomposition.
The models of silicon carbide for cast iron are generally SiC 88 and SiC 90, and the added amount is about 3% of the molten iron. The practice has proved that silicon carbide can make graphite morphology coarser and shorter, increase the spacing, and increase the number of eutectic groups. Improve the strength and hardness of cast iron, thereby improving the mechanical properties of cast products.