shrinkage of ductile cast iron
In order to product high quality ductile cast iron, there are some problems will meet in the production, generally three types, today lets know more details about one of them “shrinkage”.
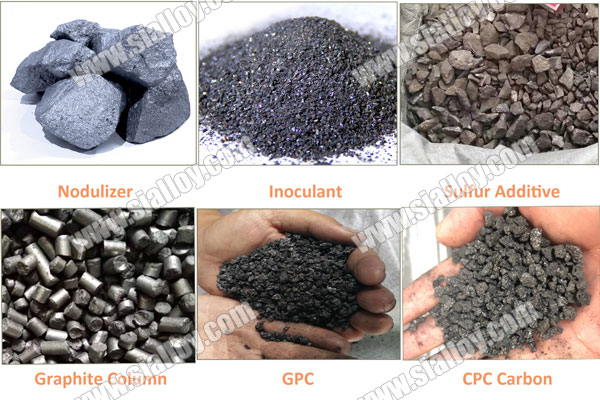
1.Influencing factors
(1)Content of carbon.increasing carbon content then will increase graphitization expansion and reduce shrinkage and porosity. In addition, increasing the carbon equivalent can also improve the fluidity of ductile iron, which is conducive to feeding.
(2)Phosphorus. The high phosphorus content is molten iron expands the solidification range, at the same time, the low melting point phosphorus eutectic can not be recharged during the final solidification, and the casting shell becomes weaker, so there is a tendency to increase shrinkage and porosity, the general factory controls the phosphorus content to be less than 0.08%.
(3)RE and Magnesium.Too high residual amount of RE will deteriorate graphite shape and reduce the spheroidization rate, so the content of RE should not be too high. Magnesium is an element that strongly stabilizes carbides and hinders graphitization. It can be seen that the amount of residual magnesium and the amount of residual RE will increase the white mouth tendency of ductile iron and reduce the expansion of graphite. Therefore, then their content is higher, they will also increase the shrinkage and porosity tendency.
(4)Wall Thickness. After a hard shell is formed on the surface of the casting, the higher the temperature of the molten metal inside, the greater the liquid shrinkage, and the volume of shrinkage and shrinkage will increase not only in absolute value, but also in relative value. In addition, if the wall thickness changes too suddenly, the isolated thick section can not be fed, which will increase the tendency of shrinkage cavity to shrink.
(5)Temperature. High pouring temperature is good for shrinkage, but too high will increase the amount of liquid shrinkage, which is not good for eliminating shrinkage and shrinkage. Therefore, the pouring temperature should be selected reasonably according to the specific situation, generally 1300~1500℃ is appropriate.
(6)The Compactness of the Sand Mold. If the compactness of the sand mold is too low or uneven, so that after pouring, under the action of metal static pressure or expansion force, the phenomenon of cavity expansion will occur, resulting in insufficient feeding of the original metal. Cause the casting to produce shrinkage cavity shrinkage.
(7)Pouring Riser and Chilled Iron. If the pouring system, riser and chilled iron are set improperly, the order of solidification of molten metal cannot be guaranteed; in addition, the number and size of risers and whether they are connected to the castings will affect the compensation of risers. Shrink effect.
2.Preventive measures
(1) Control the composition of molten iron: maintain a high carbon equivalent (>39%); minimize the phosphorus content (<0 08%); reduce the amount of residual magnesium (<0 07%); use rare earth magnesium alloys To deal with it, the residual amount of rare earth oxides is controlled at 0.02%~0.04%. (2) The process design should ensure that the casting can continuously replenish the high-temperature molten metal from the riser during solidification. The size and quantity of the riser should be appropriate to achieve sequential solidification. (3) If necessary, use cold iron and subsidies to change the temperature distribution of castings to facilitate sequential solidification. (4) The pouring temperature should be 1300~1350℃, and the pouring time of a ladle of molten iron should not exceed 25min to avoid spheroidization and decline. (5) Improve the compactness of the sand mold, generally not less than 90; the sand hits the sand uniformly, and the moisture content should not be too high to ensure that the mold has sufficient rigidity.
Anyang Huatuo has in raw materials for casting or foundry for more than 10 years, would like to share more experience with you,if want know more, welcome for contact.