problems in producing the high-strength gray cast iron
In recent years, we have researched and developed high-strength gray iron production methods that adapt to specific production conditions and different casting requirements (including thin-walled high-strength gray iron castings). In summary, there are the following four types.
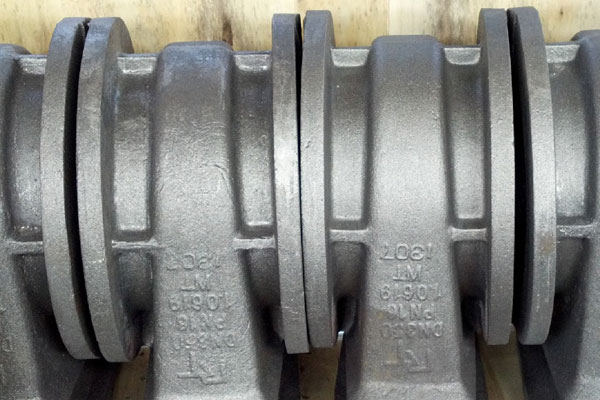
1.Strengthen the inoculation of cast iron with high-efficiency inoculants to enhance inoculation to obtain high-strength gray cast iron. Rely on high-efficiency inoculants to strengthen incubation and improve performance. The general method is: the carbon equivalent is about 3.9-4.1%, the temperature is about 1480℃, and the molten iron is required to be less oxidized. The use of Si-Ca, Cr-Si-Ca, Re-Ca-Ba, Si-Ca, Si-Fe composite, RE composite and other high-efficiency inoculants for inoculation.
2.Synthetic cast iron: it is smelted in an induction electric furnace. More than 50% of the scrap is used in the charge, and the rest is reheated iron and iron filings. The molten iron is obtained by recarburization.
The advantages of this method:
(1)The furnace section uses a large amount of scrap steel instead of pig iron, which reduces the cost of cast iron.
(2)The molten iron with low phosphorus content can be obtained, reducing the effect of phosphorus on the shrinkage and leakage defects of thin-walled high-strength gray iron such as cylinder blocks and cylinder heads.
(3)The genetic influence of pig iron can be avoided. Cast iron has good graphite morphology, high pearlite content and good mechanical properties.
3.Low-alloyed inoculated cast iron: Adjusting the chemical composition of the raw molten iron to achieve a higher carbon equivalent, add a small amount of chromium, copper, molybdenum and other alloying elements in the furnace (or package) to obtain high-temperature low-alloyed molten iron,then through inoculation treatment, a structure with fine graphite, high pearlite content and small interlaminar spacing is obtained, thereby obtaining high-strength cast iron. The alloying elements are mostly Cu, Cr, Mo, Ni, etc.
4.Adjusting the conventional chemical composition and ratio of cast iron to obtain high-strength, low-stress gray cast iron with the carbon equivalent remaining unchanged, appropriately increasing the Si/C ratio is one of the important ways to improve the strength and rigidity of machine tool castings. By adjusting the chemical composition, especially changing the silicon/carbon ratio, so that Si/C is 0.5-0.9, plus proper inoculation and alloying, high-strength gray iron castings with good comprehensive properties can be obtained.