pre-dephosphorization of liquid steel
In recent years, with the increasing demand for steel grades with high strength, high toughness, high stress resistance, and high corrosion resistance, as well as increasingly stringent quality requirements, countries all over the world are working hard to reduce the phosphorus content in steel. For example, for low-temperature steel, marine steel, hydrogen-induced fracture steel, and steel for some thick plates, in addition to requiring extremely low sulfur content, the phosphorus content in the steel is also required to be less than 0.01% or even 0.005%. In addition, in order to reduce the production cost of oxygen converter steel and reduce the generation of waste slag in steelmaking, the phosphorus content of the molten iron is also required to be less than 0.015%. Therefore, since the 1980s, many metallurgists have devoted themselves to studying the pretreatment and dephosphorization of molten iron and invented a variety of treatment methods.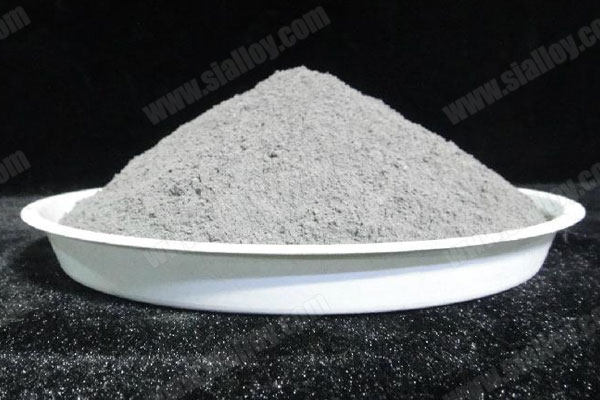
The basic principle of pre-dephosphorization outside the hot metal furnace is the same as that in the furnace, that is, it is beneficial to dephosphorization under the conditions of low temperature, high alkalinity and high oxidizing slag. Compared with molten steel, the temperature of molten iron is low, which is a favorable condition for dephosphorization outside the furnace. At this time, adding a dephosphorizer with a certain alkalinity and oxidizing ability to the molten iron can reduce the phosphorus content in the molten iron to a lower level. In some special steels with certain requirements for phosphorus content, it is necessary to increase the phosphorus content, which is generally achieved by adding Ferro Phosphorus. During oxidative dephosphorization, the phosphorus in the molten iron is oxidized to P2O5 and removed, but the melting point of P2O5 is 550 degrees Celsius and the boiling point is 605 degrees Celsius. Therefore P2O5 is a gas at the temperature of molten iron. In addition to P, there are Si, Mn, C and more than 90% Fe in hot metal. These elements will also be oxidized when oxygen is blown. In the standard liquid form, Si, Mn, C, Fe are preferentially oxidized. Phosphorus does not actually oxidize at this time, so the phosphorus in the molten iron cannot be directly oxidized to P2O5 and removed as a gas.
In order to perform dephosphorization smoothly in the oxidation process of molten iron, alkaline oxides with strong binding ability to P2O5 must be added to generate stable phosphates in order to effectively dephosphorize. Therefore, during dephosphorization, phosphorus is first oxidized to P2O5 and then combined with strong alkaline oxides to form stable phosphate. After experimental comparison, Na2O and CaO are alkaline oxides with the strongest deoxidizing ability.