how to prevent the casting cracks
Before producing castings, we always hope to be able to form at one time, but it often backfires. The castings produced have cracks. How did the casting cracks form? How should it be prevented?
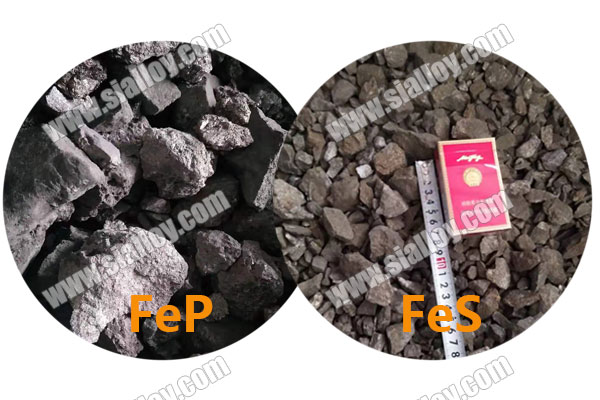
Casting cracks are mainly divided into two categories: cold cracks and hot cracks. Today we will focus on hot cracks.
Hot cracking is the shape of the crack is curved, the fracture is very irregular in the form of broken wires, and the surface is wider, the more the inside is narrower, it is a hot crack. The mechanism is: after the molten steel is injected into the cavity, it begins to condense. After the line shrinks, because the internal molten steel has not been solidified into a solid state at this time, the shrinkage is hindered, and stress or plastic deformation will occur in the casting. When they exceed the material strength limit at this high temperature, the casting will crack.
Hot cracks are cracks caused by the blocking of solid-state shrinkage of the castings when the castings are still in a state of very low strength and plasticity at the end of solidification or shortly after solidification. Hot cracking is one of the common casting defects in the production of steel castings, malleable iron castings and some light alloy castings. Hot cracks initiate at grain boundaries and extend along the grain boundaries, and their shapes are uneven, tortuous and irregular. The surface of the crack is oxidized and has no metallic luster. The cracked surface of steel castings is approximately black, while the aluminum alloy is dark gray. External cracks are visible to the naked eye and can be distinguished from cold cracks according to their shape and fracture characteristics.
Hot cracks can be divided into external cracks and internal cracks. Hot cracks that can be seen on the surface of the casting are called external cracks. External cracks often occur at the corners of castings, where the thickness of the section changes sharply, or where the local solidification is slow, and where stress concentration is likely to occur. Its characteristics are that the surface is wide and the inside is narrow, and it is tear-like. Sometimes the fracture will run through the entire casting section. Another characteristic of hot cracks is that the cracks are distributed along grain boundaries. Internal cracks generally occur in the final solidified part of the casting. The shape of the crack is very irregular, and the cross section is often accompanied by dendrites. Usually, the internal crack does not extend to the surface of the casting.
Causes of hot crack formation:
There are many theoretical and practical reasons for the formation of hot cracks, but the root cause is the solidification method of the casting and the thermal stress and shrinkage stress of the casting during the solidification period.
After the liquid metal is poured into the mold, the heat is lost mainly through the mold wall, so solidification always starts from the surface of the casting. When a large number of dendrites appear in the late stage of solidification and overlap to form a complete framework, solid-state shrinkage begins to occur. However, there is still a layer of liquid metal film (liquid film) between the dendrites that has not yet solidified. If the shrinkage of the casting is not hindered in any way, the dendrite skeleton can shrink freely without the action of force. When the shrinkage of the dendrite skeleton is hindered by sand molds or sand cores, tensile stress will be generated if it cannot shrink freely. When the tensile stress exceeds its material strength limit, cracking occurs between the dendrites. If the dendrite skeleton is pulled apart very slowly, and there is enough molten metal around the pulled part to flow into the crack in time and replenish it, then the casting will not produce hot cracks. Conversely, if the cracks are not replenished with molten metal, hot cracks will appear in the casting.
From this, it can be seen that the alloys with a wide solidification temperature range and paste or sponge network solidification are most prone to hot cracking. With the narrowing of the solidification temperature range, the hot cracking tendency of the alloy becomes smaller. Hot cracks are formed during the solidification of castings, but it does not mean that hot cracks will inevitably occur when the castings are solidified. It mainly depends on the thermal stress and shrinkage stress during the solidification period of the casting. The thermal stress in the solid-phase grain skeleton in the solidification area of the casting is easy to cause hot cracking or subcutaneous hot cracking of the casting; the shrinkage stress caused by external obstacles is the main condition for the hot cracking of the casting. The casting shell in the solidified state has its linear shrinkage hindered by external factors such as sand core, molding sand, and friction between the surface of the casting and the surface of the sand mold. There will be shrinkage stress (tensile stress) in the shell, and the hot joints of the castings, especially the sharp points of the hot joints. The thin shell formed by the corners becomes the place where the shrinkage stress is concentrated, and the casting is most prone to thermal cracking in these places.
The causes of hot cracks are reflected in the process and casting structure, including: uneven wall thickness of the casting, too small inner angle; too many forks in the lap joint, and the outer frame and rib of the casting hinder the normal shrinkage of the casting; the gating and riser system hinders the normal shrinkage of the casting. Normal shrinkage of castings, such as the casting riser close to the box belt or the high sand strength between the casting risers, which limits the free shrinkage of the casting; the riser is too small or too large; the shrinkage rate of the alloy wire is too large; the low melting point phase is formed in the alloy The elements exceed the standard, and the content of sulfur and phosphorus in cast steel and cast iron is high; the castings are thrown out of the box too early, and the cooling is too fast.
How to prevent hot cracks from occurring
1. Improve the casting structure
The wall thickness should be uniform, and the corners should be rounded to reduce stress concentration. The spokes of wheel castings can be bent if necessary.?
2. Improve the melting quality of alloy materials
Refining and degassing processes are used to remove oxide inclusions and gases in molten metal. Control the content of harmful impurities and adopt a reasonable smelting process to prevent cold cracks.?
4. Aging heat treatment
Castings with large casting stress should be subjected to aging heat treatment in time to avoid excessive residual stress causing cold cracks in the castings. If necessary, after cutting the pouring riser or welding repair, the casting should be subjected to an aging heat treatment.
Want to produce high quality castings, there are much more details need to pay attention, except the production process and the prodcution experience, also include the proper additive elements content, Anyang Huatuo Metallurgy in various alloy additive for more than 10 years, always provide qualified product include the ferro phosphorus and ferro sulfur, if any requirement welcome for consult.