how to improve the mechanical properties of gray cast iron
Heat treatment can improve the structure and properties of cast alloys to a large extent, but under the condition of gray cast iron, heat treatment can play a relatively small role. But there are other methods, such as reasonable selection of chemical composition, changing the composition of the charge, overheating of molten iron, inoculation, and micro or low alloying, etc., which can achieve good results.
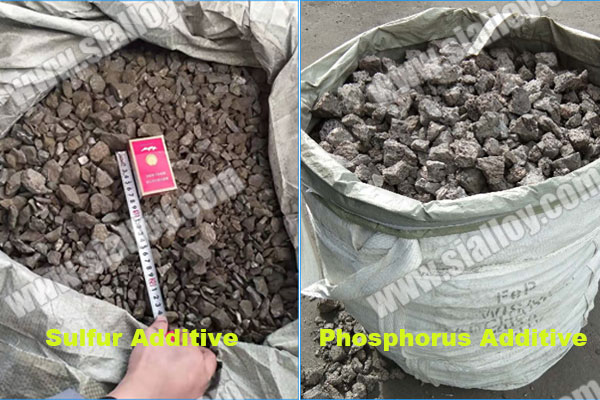
When producing high-grade gray cast iron (generally referred to as HT200 or above), in order to obtain high mechanical properties, it is necessary to reduce the amount and length of graphite as much as possible. The traditional method is to reduce the carbon and silicon content of the molten iron and increase the condensation rate of the molten iron. However, when the range is larger, D-type supercooled graphite and white mouth will appear, which will reduce the mechanical properties of gray cast iron.
Effective inoculation will promote the precipitation of graphite, thereby eliminating white mouth, thinning flake graphite and transforming supercooled graphite into non-directional uniform graphite (type A graphite), which can not only greatly improve the overall mechanical properties, but also Improve the uniformity of the as-cast structure and reduce the difference in the mechanical properties of the casting due to the uneven wall thickness, the different cooling speeds of the corners and the core. Therefore, the inoculation treatment of the molten iron is a process for the production of high-grade gray cast iron (inoculation Cast iron) essential technology. In order for the inoculation to be effective, it is necessary to meet the requirements of the inoculation for the raw iron liquid, that is, the raw iron liquid should have a lower carbon and silicon content, or the raw iron liquid should have a lower carbon equivalent. The lower the carbon equivalent, the greater the inoculation effect. Good, the higher the strength of gray iron castings; on the contrary, the higher the carbon equivalent, the poorer the inoculation effect. Since silicon can be adjusted by adding inoculants, when considering the carbon equivalent of the original molten iron, the carbon is always maintained at about 2.8%~3.2%, and the silicon is maintained slightly below the critical value that can significantly promote graphitization, and then The inoculant is added to make the amount of silicon exceed the critical value to obtain the effect of inoculation treatment.
In addition, the wall thickness and cooling rate of the casting also affect the structure of the inoculated iron castings. The chemical composition should also be considered when choosing the chemical composition. Generally, the lower limit of carbon and silicon content for thick parts, and the upper limit for thin parts. The role of manganese in high-grade gray cast iron (inoculated cast iron), in addition to the influence of sulfur, there is a special requirement, that is, with the help of it, gray cast iron can obtain pearlite structure, so high-grade gray cast iron (inoculated cast iron) The manganese content of) is generally higher. Sulfur can weaken the graphitization of the inoculant, so the sulfur is often limited to less than 0.12%. Phosphorus content generally starts from the requirements of mechanical properties and is often limited to less than 0.15%. However, some machine tool gray cast iron parts (often made of inoculated cast iron) require wear resistance, and the phosphorus content can be increased to about 0.3% to 0.5% or higher.
Anyang Huatuo Metallurgy Co., Ltd has in the raw materials such as sulfur additive, phosphorus additive, carbon additive, etc for more than 20 years, own rich experience in the production of gray cast iron, so if any confused welcome for consult.