ferroalloys furnace's refractory materials
The basic task of ferroalloy production is to extract alloy elements from ores or oxides, in theory, it can be produced by the ways of thermal decomposition, reducing agent reduction and electrolysis. At present, most ferroalloys are made by reducing with reducing agents, its production needs to be equipped with electric furnace equipment, in the smelting process, the electric furnace lining need to bear not only high temperature, but also physicochemical erosion and mechanical erosion of furnace charge,high temperature furnace gas,molten iron and slag,therefore, in order to guaranteed that the ferroalloy smelting can be effectively carried out at high temperature, it must to choose special materials for electric furnace lining, below will focus on the lining of the electric furnace.
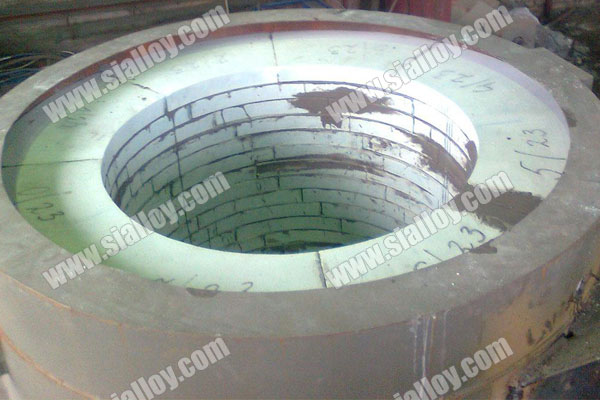
Generally, refractory materials are used for electric furnace lining, which can withstand high temperature, resist erosion and mechanical erosion of molten iron, slag, furnace gas, and can maintain the original shape, size and strength of the lining. The refractory materials commonly used in the production of ferroalloys include clay bricks, carbon bricks, high alumina bricks, magnesium bricks and magnesia, the clay bricks are mainly used to build the furnace wall lining of the exposed parts of the ore furnace or used for furnace wall or the outer layer of the furnace bottom for heat insulation and heat inulation, or for the lining of the ladle. The carbon bricks can be used as lining materials for the ferroalloys that are not afraid of carburization, but carbon bricks are easily oxidized under high temperature conditions, so they are mainly used for masonry furnaces that are not exposed to air such as furnace walls, bottom etc. The high-alumina bricks can be used for lining bricks of iron outlets of blast furnaces, blast furnace shafts, hearths, and for lining iron ladle.Magnesia bricks are mainly used for the lining of electric arc furnace walls,furnace bottoms, and low-carbon ferro-manganese iron lining, The refractory temperature of smelting magnesia is very high,therefore, in the production of ferroalloys, magnesia is often used to knot the bottom of the furnace, make or repair the furnace wall and the bottom of the furnace, and can be used as a material for plugging the eye or making the ingot mold.
So how to choose refractory materials for ferroalloy production? Generally speaking, the quality of refractory materials is judged according to five performance indicators, high refractoriness, high load softening temperature, good thermal shock stability, high temperature volume stability and slag resistance.In principle, any kind of refractory material should have five excellent performance indicators at the same time, but it is actually difficult to do. In the process of producing ferroalloys, refractory materials need to withstand the combined effects of high temperature, temperature changes, physical and chemical erosion of molten metal, slag, furnace gas, mechanical erosion and other stresses for a long time and repeatedly, however, from a local perspective, it may not necessarily withstand the above-mentioned various functions at the same time, which requires us to correctly select and use refractory materials according to the actual work of the refractory materials, so as to ensure the service life of the lining and cut costs.
Anyang Huatuo Metallurgy Co.,Ltd has devoted itself to product, process and export ferroalloys for more than 10 years, its website will share knowledge about ferroalloys from time to time, if any confused, welcome for leaving message or email us, we will contact and reply at the first time.