ferro phosphorus properties
Phosphorus has an atomic number of 15, an atomic weight of 30.97, an outer electronic structure of 3S3P, a density of 1.83g/cm3 (white phosphorus) and 2.2g/cm3 (red phosphorus), a melting point of 44°C, and a boiling point of 257°C. There are phosphides such as Fe3P, Fe2P, FeP, and FeP2. The melting temperature range of phosphorus iron containing 18%~25% phosphorus is 1100~1250℃, and the density is 5.8~6.5g/cm3.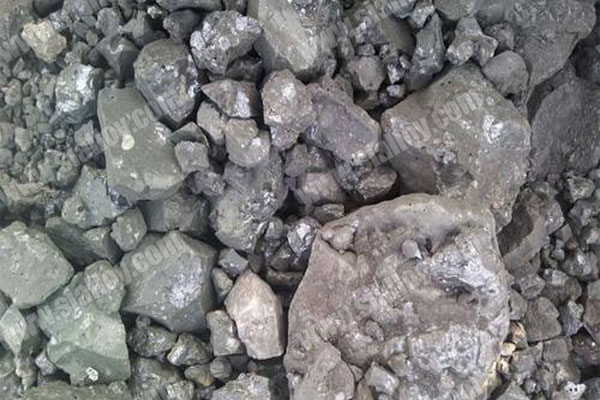
Ferrophosphorus is a compound of phosphorus and iron, and its molecular formula can be written as FenPm, where n is 1, 2 or 3; m is 1 or 2. The main iron phosphides are Fe3P, Fe2P, FeP, and FeP2. The iron phosphide products obtained from industrial production are often composed of the above-mentioned iron phosphide. Generally, ferrophosphorus contains about 70% of iron, about 20% to 26% of phosphorus, and also contains a small amount of (trace) manganese, titanium, silicon, vanadium, calcium and other elements. Ferro phosphorus products are used in the smelting of special steels in the metallurgical industry to improve the wear resistance and corrosion resistance of steel, and can also improve the casting performance of ferroalloys; in the chemical industry, ferrophosphorus can be treated with soda ash to produce sodium dihydrogen phosphate, Trisodium phosphate, and can be further processed into sodium tripolyphosphate, sodium hexametaphosphate and other products. At present, ferrophosphorus mainly comes from the yellow phosphorus industry, which is a by-product of the electric furnace method to produce yellow phosphorus. Because each ton of yellow phosphorus can only produce about 200kg of ferro-phosphorus, its output is very small and cannot meet the needs of the growing metallurgical industry and chemical industry. In recent years, some people use iron ore and phosphate ore as raw materials to produce iron phosphate by coke reduction and melting in a blast furnace with a spherical hot blast stove (hot blast temperature is 700-800℃). However, due to the production process of this method, there are The corrosion of silicon tetrafluoride gas, as well as the phosphorus vapor and the generated iron phosphate easily block pipelines and equipment, and the production equipment does not operate smoothly; the phosphorus content in the produced iron phosphorus products is less than 23%, and the output is low and the energy consumption is high.
In 1669, Brand (G. Brand) discovered phosphorus. In 1826, P. Berthier produced ferrophosphorus. In 1868, C. Brison proposed a patent for the production of phosphorus and phosphoric acid in a blast furnace. In 1929, the American blast furnace for the production of hot phosphoric acid at Victor was put into operation. In the 1870s, patents for smelting phosphorus and ferrophosphorus with electric furnaces appeared. In 1925, the first 3000kW three-phase electric furnace was built in Bitterfield to produce phosphorus. In the future, the electric furnace becomes the main equipment for the production of phosphorus. Ferrophosphorus is a by-product of the production of yellow phosphorus. The Liaoyang Ferroalloy Plant in China used electric furnaces to produce iron phosphorus in 1953, with yellow phosphorus as a by-product.