electric arc furnace steelmaking
Electric arc furnace is another steelmaking method after converter and open hearth. Because more than 95% of the world's electric furnace steelmaking production is produced by electric arc furnaces, electric furnace steelmaking mainly refers to electric arc furnace steelmaking. Electric arc furnace is an electric furnace that uses the high temperature generated by the electrode arc to smelt ores and metals. It relies on the arc generated by the discharge between the electrode and the charge to convert electrical energy into heat. When the gas discharge forms an arc, the energy is very concentrated, and the temperature of the arc zone is above 3000 ℃. In this way, various qualified steel and alloy products can be smelted.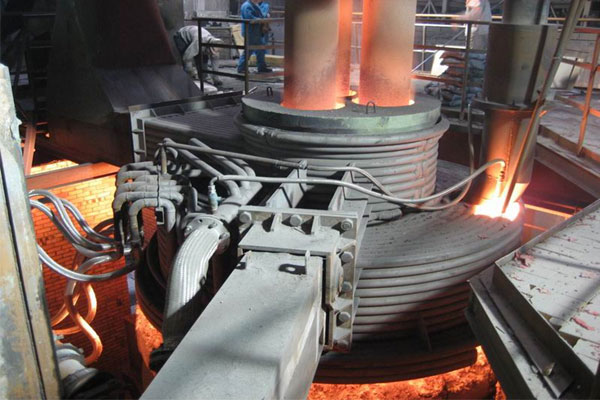
Industrial furnaces that generate electric arc heating by metal electrodes or non-metal electrodes are called electric arc furnaces. Electric arc furnaces can be divided into three-phase electric arc furnaces, consumable electric arc furnaces, single-phase electric arc furnaces and resistance electric arc furnaces according to the arc form. The furnace body of the electric steelmaking furnace is composed of a furnace cover, a furnace door, a tapping trough and a furnace body, and the furnace bottom and furnace wall are masonry with alkaline refractory materials or acid refractory materials. Electric arc steelmaking furnaces are divided into ordinary power electric arc furnaces, high power electric arc furnaces and ultra-high power electric arc furnaces according to the transformer capacity per ton of furnace capacity. Electric arc furnace steelmaking is to input electric energy into the electric arc steelmaking furnace through graphite electrodes, and the electric arc generated between the electrode end and the charge is used as the heat source for steelmaking. The electric arc furnace uses electric energy as the heat source, and the atmosphere in the furnace can be adjusted, which is extremely beneficial to the smelting of steel grades that contain more oxidizable elements. Soon after the invention of electric arc furnace steelmaking, it was used to smelt alloy steel and has been greatly developed. With the improvement of electric arc furnace equipment and the improvement of smelting technology, the development of electric power industry, the cost of electric arc furnace steelmaking continues to decline. Now electric arc furnace steelmaking is not only used to produce alloy steel, but also can be used in large quantities with materials such as Recarburizer and silicon carbide. To produce ordinary carbon steel, the proportion of its output in the total steel output of major industrial countries continues to rise.
The emergence of electric arc furnaces is equivalent to finding an alternative energy source for coal heat and allowing scrap steel to be recycled and used in large quantities to become steelmaking materials, forming a cycle of raw materials in the steel industry. Since the 1970s, the progress of the electric power industry and the development of science and technology have increased the requirements for the quality and quantity of steel, and the electric furnace steelmaking technology has also made great progress. Correspondingly, the production and usage of old raw materials such as scrap, recarburizer, silicon carbide and other raw materials that cooperate with electric furnace steelmaking technology have also reached a higher level. The temperature of the electric furnace steelmaking production process is more controllable, reducing the burning loss of easily oxidized elements, the equipment investment is small, the production is fast, and it has great advantages in refining and continuous casting, and it can use more clean energy to reduce Carbon emissions.