corrosionresistant cast iron types
According to the content of silicon, manganese, sulfur, phosphorus and other elements, corrosion-resistant cast iron can be divided into the following categories:High silicon cast iron. High silicon cast iron is divided into rare earth medium silicon cast iron. The silicon content is 10%-12%, and it contains 0.1%-0.25% rare earth elements. The hardness is slightly reduced, but the brittleness and cutting performance have been improved; copper-containing high-silicon cast iron, add 6.5% to 8.5% or 8% to 10% copper in ordinary high-silicon cast iron. Copper can improve the mechanical properties of high-silicon cast iron, increase strength and toughness, and reduce hardness. Copper-containing high-silicon cast iron is capable of turning. High silicon cast iron containing 6.5%~8.5%Cu has better corrosion resistance to other acids except for the slightly poorer corrosion resistance to 45% nitric acid in common media. Molybdenum high silicon cast iron (STSi15M03RE). Adding molybdenum can improve the hydrochloric acid corrosion resistance of high-silicon cast iron. Generally, the amount of molybdenum added is 3% to 3.5%. For high-silicon cast iron with 14.3% Si, as the amount of molybdenum added increases, the corrosion rate decreases. When molybdenum content is 3%, it is very resistant to corrosion in medium and low concentrations of hydrochloric acid, but it is still not resistant to corrosion in hot concentrated hydrochloric acid; it is a common corrosion-resistant cast iron, used in some ancient buildings or building components High-silicon cast iron can even be immortal for thousands of years. High-silicon chromium cast iron (STSi15Cr4RE), with high corrosion resistance, is suitable for the manufacture of anode castings for cathodic protection, such as equipment parts that are in contact with sea water, fresh water and other media.
Nickel austenitic cast iron: cast iron with a nickel content of 13.5% to 36%. Change the nickel content and add a small amount of other alloy elements to form different grades and types to meet the needs of different corrosive media and use conditions. Such as adding chromium, copper, molybdenum to improve corrosion resistance, adding niobium to improve weldability and so on. Various types of austenitic cast irons can be classified into austenitic gray cast irons and austenitic ductile cast irons according to the form of graphite. The metallographic structure of nickel austenitic cast iron is composed of a single austenite matrix with flake graphite, spheroidal graphite and a small amount of carbides distributed on it. Graphite morphology has no obvious effect on corrosion resistance, but after graphite spheroidization, it will significantly improve the abrasion resistance of austenitic cast iron. Austenitic cast iron has high corrosion resistance in caustic soda, bittern, sea water, marine atmosphere, reducing inorganic acids, fatty acids and other media. The corrosion resistance of nickel austenitic cast iron in alkaline medium is extremely superior.
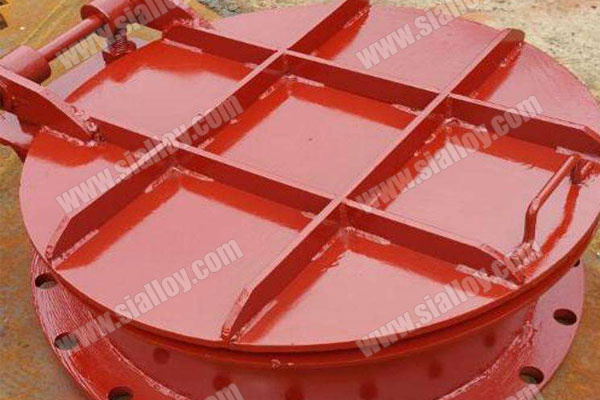
High chromium cast iron: white cast iron containing 24% to 35% chromium is called corrosion-resistant high chromium cast iron. The microstructure of high chromium cast iron is austenite or ferrite plus carbide. Generally speaking, for high chromium cast iron that does not contain a certain amount of stable austenitic alloying elements (Ni, Cu, N), ferrite is easy to obtain when the carbon content is less than 1.3%, and when the carbon content is slightly higher, it is easy to obtain Austenite matrix. Corrosion-resistant high-chromium cast iron shows good corrosion resistance in oxidizing corrosive media, while showing excellent corrosion resistance and erosion resistance in corrosive media containing solid particles.
Aluminum-containing cast iron: Cast iron containing 3.5% to 6% aluminum is used to manufacture pump valve parts for transporting corrosive media such as hydrazine ammonia mother liquor, ammonium chloride solution, and ammonium bicarbonate mother liquor. In the ammonia mother liquor without crystals, the corrosion rate of aluminum cast iron is 0.1 to 1.0 mm/a. In the soda solution containing crystals, in order to improve the wear and corrosion resistance of aluminum cast iron, 4% to 6% Si and 0.5% to 1.0% Cr can be added to aluminum cast iron to obtain aluminum silicon cast iron.
Low-alloy corrosion-resistant cast iron: mainly includes copper-containing cast iron, low-chromium cast iron, and low-nickel cast iron. The copper content of 0.40% can reduce the corrosion of cast iron in the atmosphere by more than 25%, and the effect is better in the atmosphere containing concentrated sulfuric acid flue gas. A centrifugal pump that uses cast iron containing 0.4% to 0.5% Cu to transport sulfuric acid has a service life that is 30% longer than that of ordinary cast iron pumps. In the cold or hot heavy oil with high sulfur content, adding copper can reduce the corrosion of cast iron, so copper-containing cast iron can be used in the petroleum industry. Adding a small amount of tin or antimony to copper-containing cast iron can further improve its corrosion resistance; low-chromium cast iron. Adding 0.5% to 2.3% Cr in cast iron can weaken the corrosion of cast iron in flowing seawater, reducing the corrosion rate by about 50%; low-nickel cast iron. Adding 2% to 4% of nickel to cast iron can improve the corrosion resistance of cast iron in alkali, salt solution and seawater.