carburizer for casting
Carburizer is a ferroalloy product used to increase the carbon content. The carburizer can be divided into graphite carburizer, petroleum coke carburizer, coal quality carburettor, etc. The carbonizer product produced by the process, using an electric furnace to perform the casting process by adding metal charge is not enough to preserve the carbon element content in the molten iron. In the case of this carbon element content loss, it is necessary to use casting Carbon agent to ensure that the content of carbon in the molten iron meets the production standard. From this, we can see the important role of casting carburizer in casting. Let's let the editor talk about the benefits of casting carburizer for everyone. It is said that many Many casting masters who have been working for many years have said that they don't even know!
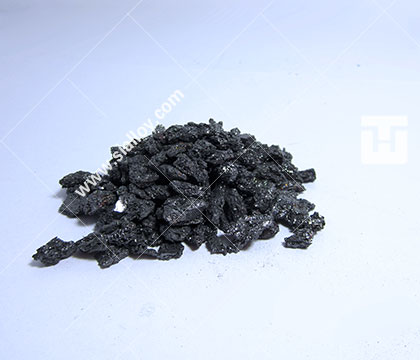
The graphitization of unmelted particles in the carburizer for casting
The use of casting carburizers in casting can effectively generate and promote graphite cores. A certain proportion of casting carburizers is added to the molten iron. Some are dissolved in the molten iron, but some of the unmelted casting carburizers are still melted. The carbon agent will be carbon in the form of graphite and will be entangled into the molten iron water flow in the form of particles. Among them, there are some large particles of casting carburizers. When energized, these unmelted casting carburizers will be firmly adsorbed in The center of the furnace wall of the smelting furnace, but if the power is turned off, these unmelted casting recarburizers will be suspended. After laboratory observations, the very small particles of casting recarburizers in the process of graphite melting, even when the power is stopped Can be suspended in molten iron.
These tiny particles of casting carburizing agent are close to the material constituting the eutectic nucleus of iron alloy. The suspended casting carburizing agent particles are beneficial to the formation of graphite core, which can prevent the white mouth phenomenon caused by excessive cooling during casting!
The size of foundry carburizer is the main factor affecting the melting of the carburizer into the molten iron. Although the carburization rate after 15 min is the same, the carburization time of the carburizer for casting that reaches 90% is quite different. It takes 13 minutes to use casting recarburizer without particle size treatment, 8 minutes to remove fine powder, and only 6 minutes to remove fine powder and coarse grain. The particle size has a greater influence on the carbonization time. It is not good to mix in fine powder and coarse particles, especially when the content of fine powder is high.
The purpose of adding casting carburizer in the smelting process is to increase the carbon content, which can better increase the graphitization expansion, thereby reducing the occurrence of shrinkage shrinkage and shrinkage of castings. The recovery of magnesium from casting carburizer for magnesium The rate also has an important effect. In addition, the use of casting carburizers increases the carbon content of the molten iron, which can improve the fluidity of ductile iron, which is conducive to replenishment. After a large number of experiments, it has been concluded that the casting casting needs to produce high-quality castings. The carbon content is c>17% si> 39%.
It can be seen that the benefits of casting carburizers are really more. Now more and more foundry manufacturers are using casting carburizers as smelting materials to avoid the quality of castings and important materials to prevent white mouthing. I believe In the future, the carburizing agent for casting will develop better and use better!