carbon additives recarburizer
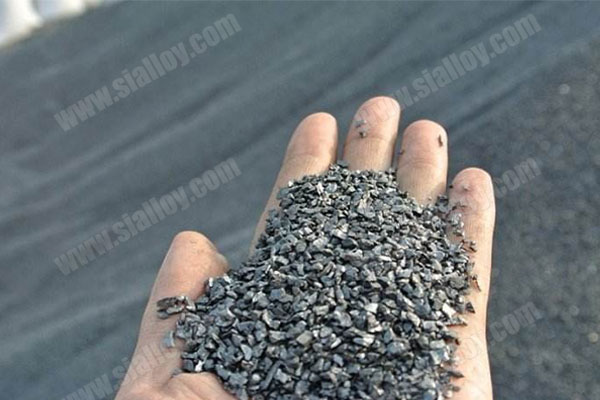
The classification of the carbon additives recarburizer for casting can be divided into several different types according to different materials specifications of carbon additives recarburizers.
According to the casting use, it is divided into: spheroidal graphite iron recarburizer, gray cast iron recarburizer, cast steel recarburizer, special steel recarburizer.
Ductile iron carbon additives recarburizers are generally selected to use graphitized high carbon and low sulfur products. The carbon content is generally required to be above 98.5. The sulfur content is less than 0.05%. The main components are graphitized petroleum coke, graphitized electrodes and the like. This recarburizer has the highest absorption rate and the fastest absorption rate.
The main technical indicators of gray cast iron carbon additives recarburizer and ductile iron recarburizer are the sulfur content. Sulfur is generally required to be less than 0.5%. The carbon content is available in various sizes between 90-98.5. Its main materials are petroleum coke, calcined coal and the like. The absorption rate of this kind of recarburizer is slightly lower, generally about 85%.
There are many types of cast steel carbon additives recarburizers, and the types of materials are complex. Generally, large steel mills choose a variety of recarburizers according to different steel grades, but the general materials are calcined coal, or graphite balls, which are also broken with natural graphite. The content ranges from 75-99.
The special steel carbon additives recarburizer is mainly used in the manufacture of brake pads, and the core wire is manufactured. Most of the petroleum cokes with 0-0.5 or 0.5-1MM grain size are used.