calcined coke carburizer
The main component of calcined coke carburizer is carbon element, and its role is carbon increase as the name suggests. However, the quality of different carburizers is not the same. The higher the carbon content, the lower the basic impurities (basic impurities generally refer to ash, volatiles, moisture, etc.). Another is the content of sulfur and nitrogen in ferroalloy components. The role of sulfur is basically clear to many people. A certain amount of sulfur in cast iron can better update the physical properties of iterative castings. In recent years, the nitrogen content has also been extensively studied by everyone. The nitrogen content is too high, resulting in nitrogen pores, the nitrogen content is too low, the hardness of the casting is not up, and the ferrite is much.
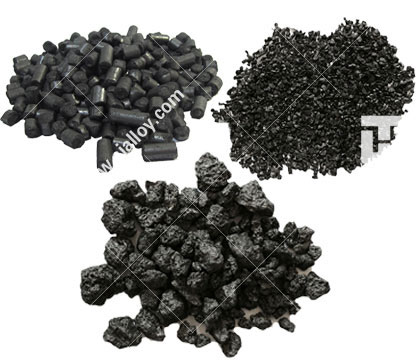
What are the functions and requirements of coke carbonizer after iron alloy calcination?
The role of calcined coke carburizer is used to cast cast iron and cast steel. The casting will have a requirement for carbon. Then the carburizer is used to increase the carbon content in the molten iron. The commonly used furnace materials in smelting are pig iron, scrap steel, and furnace furnace materials. The carbon content of pig iron is high, but the purchase price is higher than that of scrap steel. Therefore, the amount of scrap steel added and the addition of high-quality carburant reduce the amount of pig iron added, saving the production cost and satisfying the production requirements. need. Each batch of carburizer is slightly different. You want a specific percentage, which is unrealistic. Other components include ash, moisture, sulfur, and phosphorus. Significant carburizer generally refers to graphitized recarburizer. Under high temperature conditions, the arrangement of carbon atoms is in the microscopic form of graphite, so it is called graphitized recarburizer. Graphitization can reduce the content of impurities in the carburizer, increase the carbon content of the carburizer, and reduce the sulfur content, so the price is relatively high.
Conventional particle size of the calcined carbonaceous agent after calcination: small particle size: 0-1mm, 0.5-2mm, 0-2mm, etc .; medium particle size: 1-3mm, 0-3mm, 0-5mm, 1-5mm, 3-5mm, 3 -8mm, etc .; Large particle size: 8-30mm, etc., but the actual application requirements also have various particle sizes, and the screening plant can sort out various particle sizes
If the particle size of the carburizer is too fine, it is easy to burn, and if it is too coarse, it will float on the surface of the molten steel and will not be easily absorbed by the molten steel. The particle size of the induction furnace is 0.5-6mm, of which the particle size of steel and other ferrous metals is 1-8mm, the high carbon steel requires low nitrogen, the particle size is 1-5mm, etc. The detailed judgment and selection of the model and other details.
The general requirements for smelting or cast iron recarburizers are:
1. The fixed carbon should be high, the content of ash, volatiles, sulfur, phosphorus, nitrogen and other impurities should be low, and should be dry, clean, and the particle size should be moderate.
2. Its fixed carbon> 98%, volatile matter< 1.0%, S < 1%, moisture < 0.5%.